CNCフライスで、ルアーのシリコン型の原型を加工する時の材料用の型を作ることにしました。
型、型と訳の分からないことになっていますが、そういう事です(どういうこと?)
今までは、適当な大きさのプラスチックのケースにレジンキャストを流し込んで作っていました。
ただ、このケースの全長が130mmあって、このままではフライスのバイスで掴めなかったんです。
バイスは120mmしか開きません。
なのでいつも10mmほどカットしてから使っていたのですが、これが結構面倒でして…
電動工具を使ってカットするので仕事から帰って来て夜中に作業するのは厳しい…
さらに、最近は仕事の都合でルアー製作の時間があまり取れなくなっているので少しでも時間を掛けずに済むように、少し手間とお金が掛かるが作っちゃいます。
今まで使っていたケースがこれです。
幅90mm、全長130mm、厚みはレジンキャストの量で調整して作っていました。
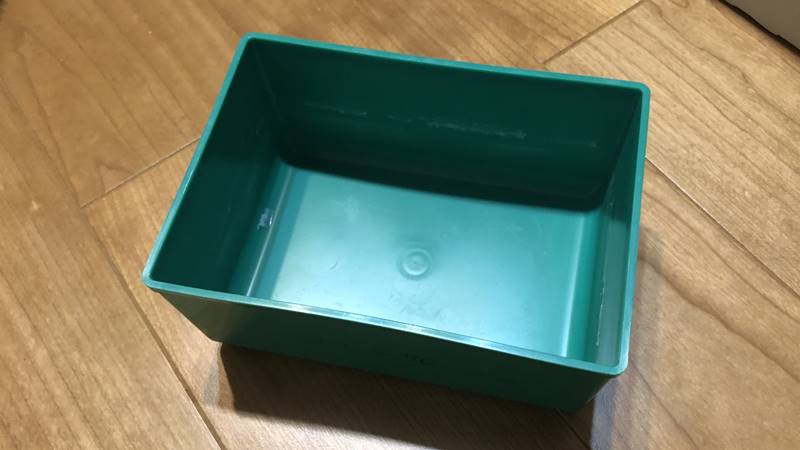
なかなか手頃なサイズで便利に使っていたのですが少し難点もあって、ケース底の部分の大きなR形状と、既製品なので抜き勾配があります。厚みの上と下で寸法が変わってしまうので多少ですが使いにくかったですね。
これらを解消するために作ってみたのがこれです。
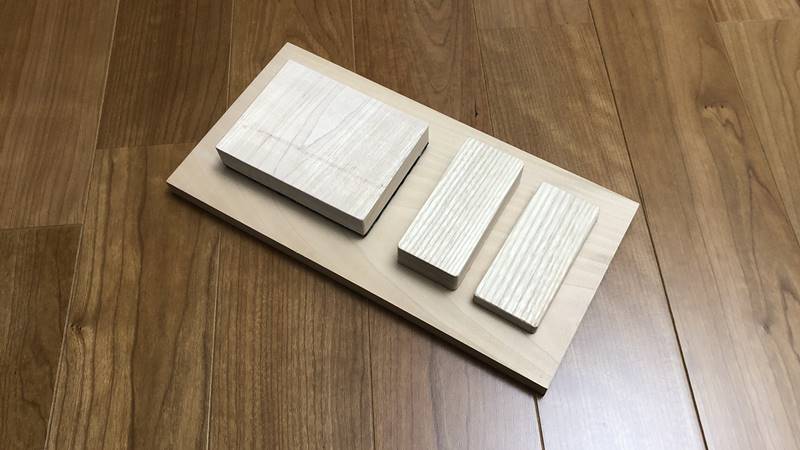
なんだこれ?
って感じですかね。
左端の大きいのが90mm X 120mmサイズでバイスいっぱいで使用する為のもので、他の2個はついでによく使うサイズのものを準備しました。
これに、いつものようにアルミテープを巻いて枠を作ります。
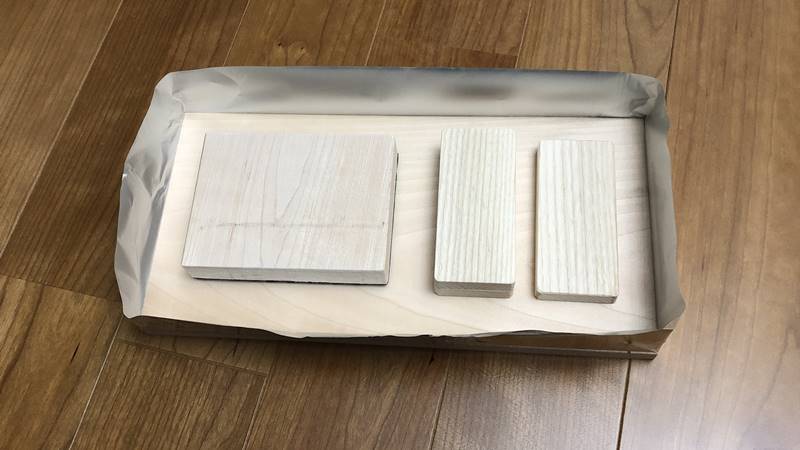
で、これにシリコン大量投入!!
シリコン1.5kg使っています…
もし、失敗すれば大損害です。
絶対に失敗は許されません!!
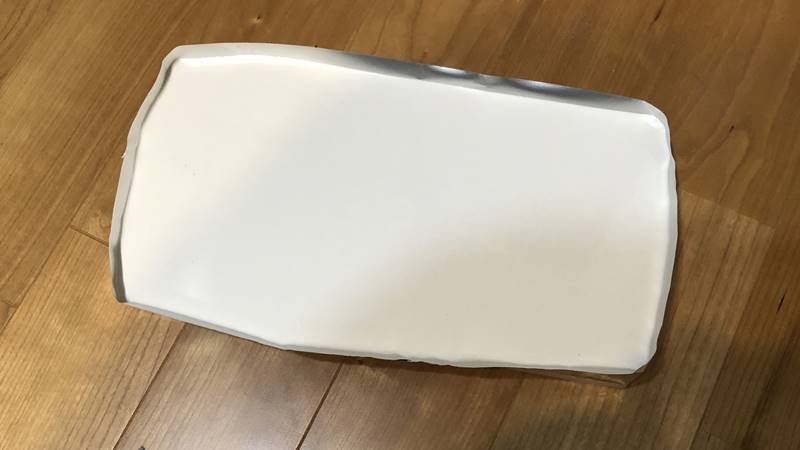
無事に成功しました!
ただ、これほどデカイ型になるとシリコンを原型から剥がすのが大変でした。
無理してシリコンが割れてしまいでもすればショックで立ち直れなくなるかもしれないと思い、細心の注意で挑みましたね。
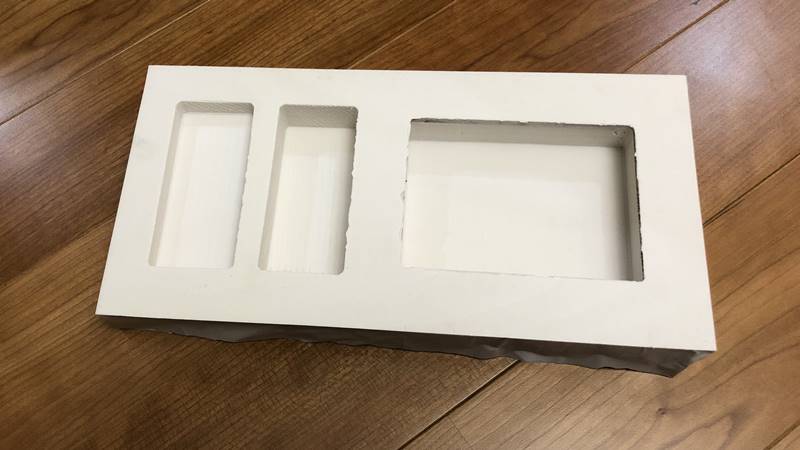
早速試しに材料を作ってみます。
レジンキャスト硬化中です。
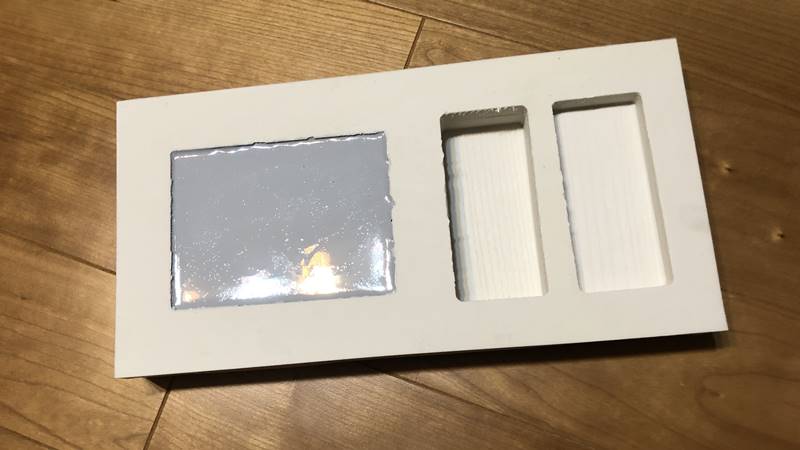
材料も無事に完成!!
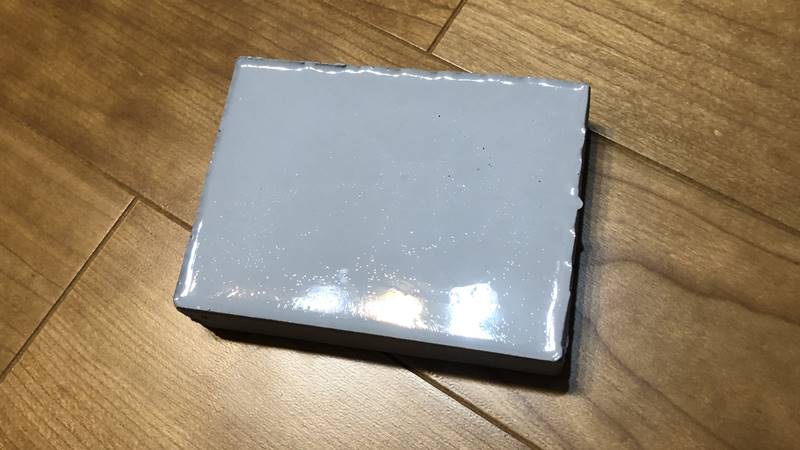
これで、いつでも材料の製作が出来るようになりました!
こういった物って、作るまでは面倒くさかったりお金が掛かったりして作るのを躊躇してしまうのですが、作ってしまえばやっぱり作って良かったなーって思いますね。
たった10mmカットするだけとはいえ、毎回同じことをするのは苦痛に感じてきます。
同じ作業の繰り返しなら、やはりあると楽ですし便利です。
他にも使いやすそうなサイズの型も作ろっかな。
といっても、お金が掛かるので直ぐには無理なんですが…
それではお疲れさまでした!
コメント