今回は、小型CNCフライスを使ってルアーの原型を作っていきます。
長くなりますので何回かに分けて記事を書いていきます。
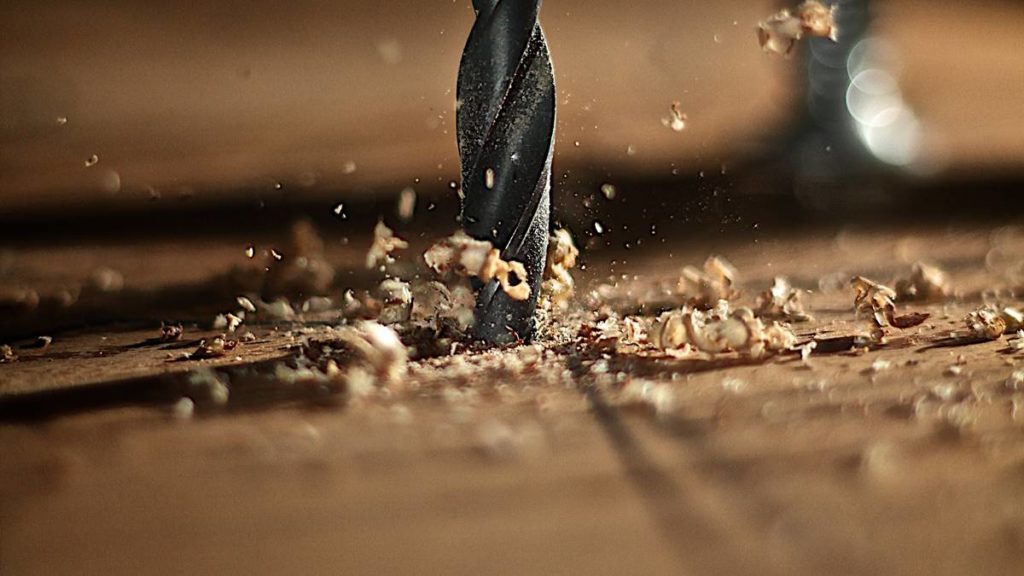
CNCフライスで出来る事
CNCフライスを使えばどんな加工が出来るのか?
小型のCNCフライスでは、アルミ、真鍮くらいまでの金属でしたら問題なく切削できます。
金属が削る事が出来れば、スピナーベイトのブレードや、バズベイトやスウィッシャー(スイッシャー)のペラやメタルバイブなど、ルアーに使う金属パーツが容易に加工できます。
しかも、手作業でするより早く正確に同じのを幾つも作る事が出来るようになります。
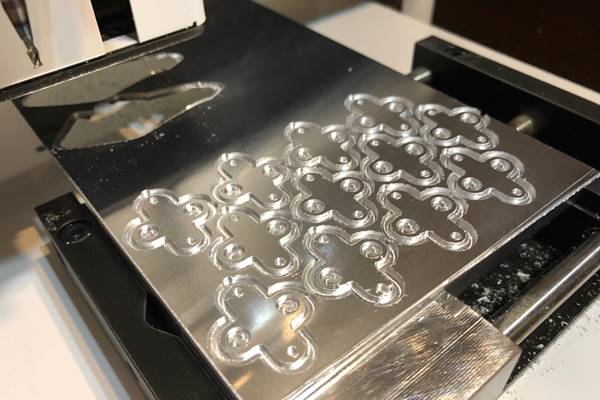
次に、シリコン型の原型を作ったり、ルアーそのものを作ったりする3次元加工
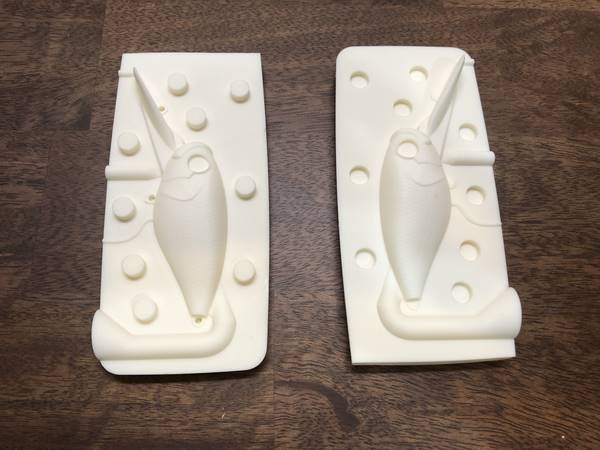
このような加工が出来ます。
もちろん、ルアーに限らず色々なものを作る事が出来ます。
CNCフライスの説明
そもそも、CNCって何?
という人もいると思いますので簡単な説明から始めます。
CNCとは、Computerized Numerical Control( コンピュータライズド・ニューメリカル・コントロール )の頭文字をとったものです。
日本語では、コンピューター数値制御ですね。
プログラムでコンピューターに指示を出して、その通りに加工してもらう機械です。
仕事で使うような大型の物は機械とコンピューターが一体になったものです。
今回使うのは、それのホビー版の小型卓上CNCフライス盤といって、コンピュータの代わりにパソコンを使って動かします。
CNC加工に必要なもの
- 小型CNCフライス盤
- CNCソフト(コントローラー)
- パソコン
- CAD
- CAM
- エンドミル
小型CNCフライス盤
私が使用しているのは、オリジナルマインド製のKittMilシリーズのQt100という機種です。
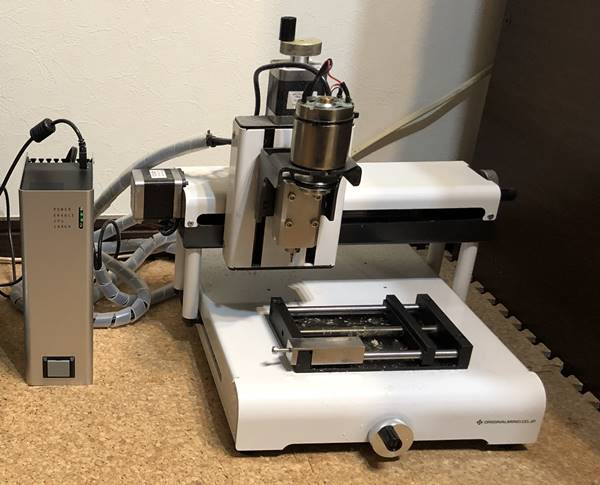
現在は、生産中止になっているようですね。
機械の購入を検討されている方は、以下の点に注意して機種を決めてください。
- X,Y,Z軸のストローク(可動範囲)
- 取り付け可能材料高さ
X,Yのストロークは当然作れるルアーの最大サイズ(実際にはこの寸法より狭くなります)になります。
注意が必要なのはZ軸のストロークと取り付け可能材料寸法です。
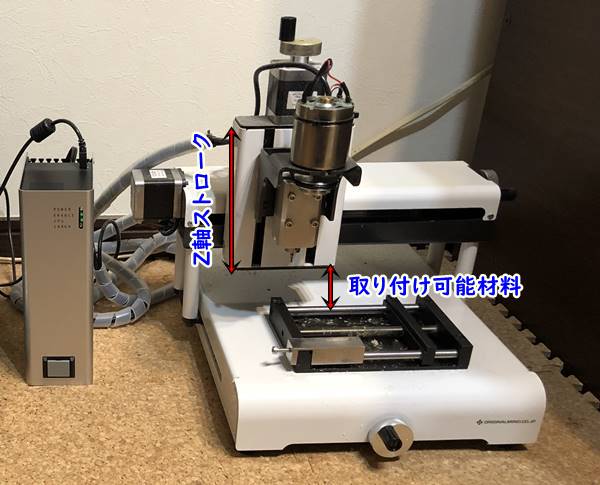
上の写真で説明しますと、Z軸に主軸モーターが付いている黒い台座があります。
Z軸が上下に動くのは、この部分だけです。
黒い台座の後ろにある白い四角い部分は上下には動きません。
つまり、どんなにZ軸のストロークがあっても、実際に加工できるのは取り付け可能材料の寸法までです。
これを超える材料をセットした場合、X,Y軸が動いた際に材料にぶつかってしまいます。
仕様に書かれている寸法はテーブル面からの寸法ですので、写真のようにバイスをセットするとさらに狭くなります。
案内形式(摺動面)は、
スライドシャフト – ドライブシュ
↓
リニアシャフト – リニアブッシュ
↓
リニアガイド
下に行くほど価格が上がります。
送り形式は、
メートルねじ
↓
台形ねじ
↓
ボールねじ(ボールスクリュー)
下に行くほど高精度になり価格が上がります。
求める精度と予算に合わせて決めてください。
個人的には、スライドシャフト – ドライブシュ以外ならどの組み合わせでも良いのではないかと思います。
CNCソフト(コントローラー)
パソコンと機械のやり取りを制御するためのソフトになります。
私は機械購入時に含まれているUCBCNCというソフトとコントローラーを使っています。
パソコン上でこのソフトを起動してから、プログラムを読み込んでコントローラー側に指令を送って加工する事になります。
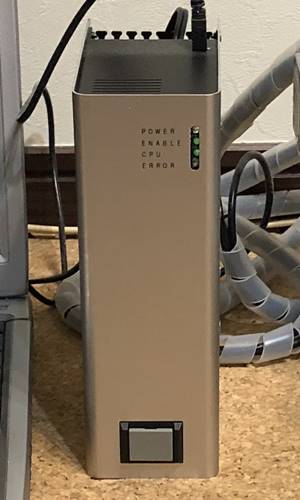
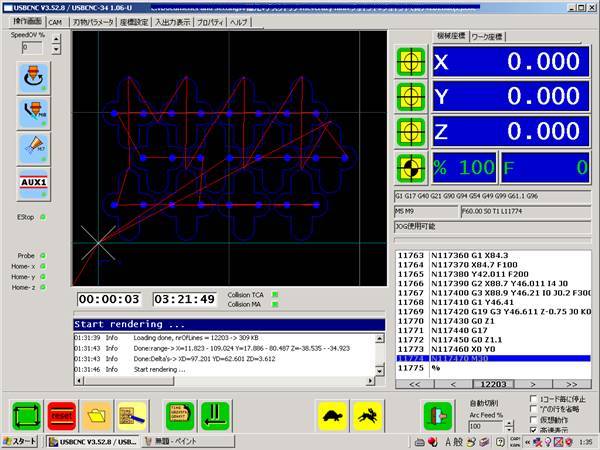
このソフトを使ってプログラムを読み込み、計算してコントローラーに指令を送ります。
コントローラは受け取った指令通りに機械のモーターを動かします。
パソコン
パソコンはCNCソフトの推奨条件さえ満たしていれば何でもいいです。
CAD
CADとは、パソコン上に図形(モデル)を描くソフトです。
2次元と3次元が有りますが、ルアー作りでは3次元CADを使用します。
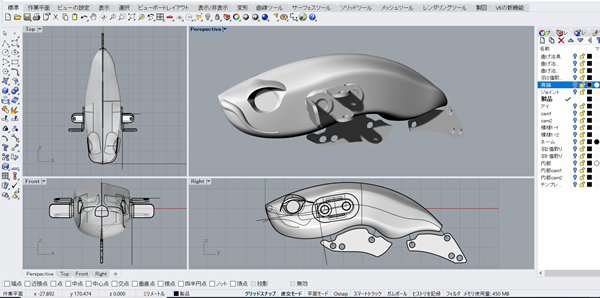
私が使用しているのは、Rhinocerosという3次元CADです。
ここで作ったモデルをCAMソフトへ渡して、機械に理解できるプログラムへ変換してもらいます。
CAM
CAMの役割は、CADで描いたモデルをCNCフライス盤が理解してくれるプログラムに変換する事です。
実際の加工は、エンドミルという刃物を回転させて加工していくのですが、この刃物をX方向に幾つY方向に幾つ動きなさいといった指示を出すための命令と座標を作成してくれます。
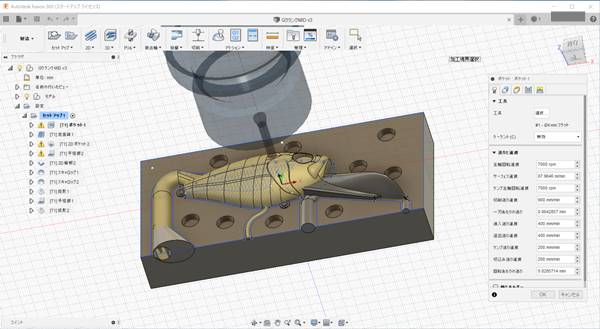
私が使っているCAMは、Autodesk社のFusion360です。
このCAMは、CADCAMといってCADとCAMの両方が使えます。
しかも趣味で使う場合は無料です。
今から始める方は、このソフトだけでCADとCAMが両方無料で使う事が出来ます。
本来、CAMというのは製造業の会社が仕事で使用するものですので数百万という価格がします。
それを、無料で使用させて頂けるのは本当に有難いことですね。
エンドミル
エンドミルとは材料を削る為の刃物の名称です。
フラットエンドミル、ボールエンドミルなど刃先の形状が違うタイプが幾つかあります。
3次元加工の加工では主に、
荒取りでフラットエンドミル
仕上げでボールエンドミル
を使用することが多いです。
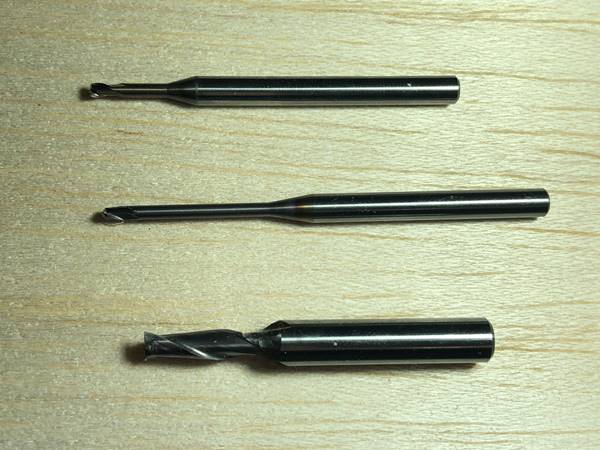
このような刃物を取り付けて加工していきます。
今回は、ここまでの説明にしておきます。
次は、最初の手順CAD編の予定です。
CAD編
CAM編
CNCソフト編
の流れで記事を書く予定にしています。
コメント
教えていただき、ありがとうございます。
おじいちゃんに、monchiさんにすごく丁寧に教えてもらったことを伝えたら、「そんな親切な人がいるんだぁ。ありがたいねぇ」って言ってました。
monchiさんのアルミのブレード制作の記事を参考にしながら作ってきたのですが、平行ピンを刺すだけでもすごく工夫されているんですね。金型って、突き詰めれば突き詰めるほど、奥が深いものなんですね。
以前教えていただいたように、なんとかオス型を貫通した穴を作って平行ピンを圧入した方がベストのように思いますが、たとえば、monchiさんは以下のような方法をとられたことはありますでしょうか?もし実践されたことがあったら、その方法の問題点を教えていただけますと幸いです。
例)
○平行ピン 直径3mm 長さ10mm
○オス型(ブレード部分を除いたところの高さ10mm)に、深さ6mmで直径2.99mmの穴を掘る
○メス型(ブレード部分を除いたところの高さ10mm)に、深さ4.0〜4.5mmで直径3.05mmの穴を掘る
上のように、オス型とメス型両方、穴は貫通させずに、平行ピンを差し込むという方法です。
親切ですか(笑)
なんか、くすぐったいですね。
趣味でやってる事に特に機密事項などないですからね-
ブログやってて、「それは教えられません」ってのもつまらないですし。
アドバイス出来る事だったら時間があれば幾らでもしますよ。
実際、私もネットで解らないことを色々と調べたりしますからね。
で、質問されていた事への回答ですが。
全く同じ条件の加工はやっていませんので想像も含めて答えます。
平行ピン 直径3mm 長さ10mm
これは、長さはこれで十分か?
という事ですか?
これはケースバイケースで違うのでなんとも言えないです。
今回の場合は大丈夫だと思いますが、使ってみて問題があったら長いのに変更するしか無いですね。
φ2のエンドミルでφ3の穴を深さ6mm加工するのはリスクが高いかもしれません。
エンドミルの径と仕上り径が近くて深さも6mmと深いので切粉の排出が悪くなります。
こういう状況だと、どうしても切粉の噛み込みが発生しやすくなります。
噛み込みによって仕上がりが悪くなったり刃物に負荷がかかり過ぎて破損する可能性もあります。
特にQT100は主軸のパワーが足りないので心配ですね。
削れないことも無いかもしれませんが、途中途中で切粉の処理をした方がいいかもしれません。
私としてはリスクを覚悟してまで行う加工では無いかなと思います。
メス型の方の穴の深さはもう少し余裕を見た深さにしておいた方がいいと思いますよ。
ピン長さ10mm
圧入6mm
出っ張り4mm
ですよね。
深さ4.5mmは大丈夫かもしれないですが4mmだと圧入側にもし5.9mmとかしか入ってなかった場合は型をピッタリ閉じる事が出来なくなります。
ピンもキッチリ10mmとは限らないですし。
穴を貫通させた方が良い理由として、もしもピンを抜きたい時があった場合(もう少し長い方が良かったかもという場合や、圧入時にピンが曲がってしまった等)に貫通させていないと抜くのが困難になります。
貫通させていれば反対側から簡単に押し出す事が出来ます。
以上の事から出来れば3mm程度の深さの案内だけ加工してボール盤で貫通穴をあけることをお勧めします。
ボール盤はお持ちですか?
もし持っていなくてボール盤の購入に抵抗があれば、一度これと同じ条件の加工にチャレンジしてみて判断されてもいいかもしれません。
「これはヤバそうだボール盤買った方が結果的に安く済みそうだ」と思ったら購入!
全然問題なさそうだと感じたらそれはそれで良いでしょうし。
でも、持っていれば何かと便利なのは間違いないです。
以前切削について質問させていただいたタカです。その際はありがとうございました。
フライスに不具合があることがわかり、その修理に時間がかかってしまいました。時間が経ってしまったのですが、教えていただいた設定で一応真鍮の切削はできました。
ただ、残ったバリがあまりにも大きく、切削がちゃんとできていないのではないかと感じています。
そこで1つお願いなのですが、そのバリの写真を見ていただけませんでしょうか?
もし見ていただけるようであれば、方法として、私の方でTwitterのアカウントを作り、そこにバリの写真をアップして、こちらのコメント欄の入力欄の「サイト」の方に、そのURLを貼り付けてみたいと考えています。
ご検討いただけますと幸いです。
どうぞよろしくお願い致します。
タカさん
お久しぶりです。
フライスの修理大変でしたね。
直ったようで良かったです。
写真はメールで送ってもらって構わないですよ。
onefish215@gmail.com
こちらにお願いします。
バリというのが薄皮一枚残して加工した部分のことでしたら、設定値の問題か、ステッピングモーターの脱調が原因の可能性があります。
写真拝見しました。
鯛焼きの写真は少し笑ってしまいました(^^)
問題のバリですが、見たところフライスの問題というより刃物の状態が良くないように思います。
上に盛り上がる現象は、刃物が素材を削ることが出来ずに外側に押し退けてしまう事によって起きます。
例えば粘土などに横から指を押し付けると上に盛り上がりますよね。
これが切れ味の良いカッターなどを押し付けても盛り上がらずに刃が入っていきます。
これと同じ状態です。
例えが判りにくかったらごめんなさい。
下に膨らんでしまうのも同じような理由で、刃先の角がダレたり欠けていたりすると、その部分は削ることができずに下方向に押す力が発生します。
少し気になるのは、かなり下に膨らんでいますが捨て板は使用していますでしょうか?
使用していてこの状態になっていたら捨て板の方にも凹みなどがあると思うのですが、そちらは大丈夫でしたか?
それと刃物の種類ですが、削った後がボールエンドミルっぽく見えますが、使用しているエンドミルはフラットエンドミルですよね?
もしボールエンドミルを使っているのでしたら、このような加工には不向きな刃物ですのでフラットエンドミルで加工してみてください。
比較で添付されている私の写真(写真6)のバリも、刃物の切れ味が悪くなってきている状態です。
新品の状態だとこのバリも無いくらい綺麗に仕上がります。
それから、お礼などは考えないでください。
私が何か困っている時などに、逆にタカさんの知識や知恵をお借りできたりと、お互いに助け合えたら良いなと思っています。
ありがとうございます!
昨日のトップの高さについてのアドバイスをいただいて、よく切削できていなかった根本的な原因のうちの1つがわかったように思います!
最初の削り始めるトップの高さって、後々の切削途中にも影響するように思いました。最初からしっかり削れていないと、負債のようにストックが残って、負荷がかかりやすくなるように思います。
本当にありがとうございます!!
確認していただき、ありがとうございます。
捨板は、アルミ10mm厚のものを使用しており、アルミと真鍮を、0.1mmの両面テープで接着しています。
アルミの方までは凹みはありませんが、両面テープの方に凹みがありました。
ボールではなく、フラットになります。
写真のような大きなバリは、monchiさんはこれまでに経験されたことはありますでしょうか?
以前ご紹介いただいたフラットエンドミルAL2Dを使用したのですが、購入してから数回しか使っておりません。
ただ、2ヶ月くらい前に使ったときは、フライスの方に問題があり、うまく切削できず、切削を継続したらエンドミルが折れる心配があり、そのときは中断しました。
そのときに刃が傷んだと考えた方がよろしいでしょうか?
また、エンドミル1本分は、丁寧にミスなく使用していたとしても、そんなに長く使用できるものではないと考えた方がよろしいでしょうか?
以上どうぞよろしくお願い致します。
エンドミルは私と同じ物を使っていたのですね。
失礼いたしました。
バリですが、私はそこまでの状態になった事は無いですね。
2ヶ月前にエンドミルが折れるかもしれないと思うほどの状況だったのでしたら、その時に刃先が欠けたりしている可能性はありますね。
一度、刃先の確認をしてみた方がいいですね。
その時(修理された時)のフライスの問題はスピンドル部分ですか?
スピンドルに振れがある可能性もあります。
振れが大きいと1刃あたりの切削量が多くなったり、刃の裏側(2番面といわれる逃し面)が当たってしまたりして綺麗に切削出来なくなります。
振れのチェックもしてみた方がいいですね。
QT100は何年も前の機種ですので、長い間ご使用されているのでしたらベアリングにガタが出てきている可能性もありますね。
まともに削れていた場合、数回の使用でエンドミルがダメになる事は無いと思います。
ですが、使用回数が少なくても合計の切削距離が長いとダメになるかもしれません。
ですが、タカさんはまだそれほど削っていないと思うので、これは関係なさそうですね。
ただ、エンドミルも残念なことに個体差?があって、稀にですが外れもありますので一概に無いとも言い切れません。
ちなみに私が今使っているエンドミルは1年近く使っています。
もう何十回も使っていますが、まだまだ使えます。
先日はアドバイスいただき、ありがとうございました。
練習として、0.5mmの厚さの真鍮板を削ってみたのですが、真鍮板自体が伸びて、バリが大分残ってしまいました(切削条件としては、切込み0.05mmで切削速度はF200にしていまして、他の速度は、大分遅めに設定していました)。
原因として、ボトムを0.5mmよりも深い0.6mmに設定し、ボールエンドミルで切削したせいかなとは思っているのですが、真鍮板を切削する場合は、エンドミルをボールではなく、フラットにした方が良いでしょうか?
また、エンドミルの刃数は今は2枚なのですが、真鍮やアルミを切削するのに、3枚または4枚の刃数のフラットエンドミルを使われていますでしょうか?
頑張っていますね~
私の真鍮の切削条件は
切り込み:0.05mm
送り速度:F400
刃物 :フラットエンドミル超硬φ2(日進工具AL2D 2DLC)
です。
AL2D 2DLC(型番)はアルミと真鍮の加工の時に使います。
特にアルミの5000番など軟らかい素材をドライ加工する時には切削時に刃物に溶着する可能性があるので仕上がりが悪くなったり刃物の破損も考えられます。
DLCコーティングは摩擦を抑えてその辺の問題を解消してくれます。
それと私は刃物は超硬のものしか使っていません。
真鍮が伸びるという状態がよく分からないのですが曲がってしまうということですか?
ボールエンドミルを使って板厚より深く加工しておられるようですが、真鍮板のクランプはどうされているのでしょうか?
これだと必要なパーツと板が切り離されてしまってパーツが飛んで行ってしまうと思うのですが?
それと板厚0.5mmをボールエンドミルで深さ0.6mm加工だとパーツの側面にR形状が残ってしまうと思いますが大丈夫なのでしょうか?
私の切り抜き加工の方法は、10mm厚くらいのアルミや鉄の捨て板(実際は捨てませんけど)に両面テープを使って加工する板を固定しています。
加工する深さは板厚マイナス0.05mmです。
板厚1mmだとすると0.95mmの深さまで加工します。
こうする事で0.05mmのペラペラが残ってパーツが板から切り離されることなく加工できます。
注意したいのは両面テープを削らないようにする事ですね。
刃物が切れなくなります。
私はボールエンドミルは2.5D/3D形状の中仕上げか仕上げ加工にしか使用しません。
それ以外はフラットエンドミルを使います。
刃数は2枚刃で構わないですよ。
ありがとうございます!
自分もFusionを使うようになって、わからないことをこんな感じで教えてもらい、新しい発見や気づきを得られるのですごく楽しいです。
とてもありがとうございます!
ボディにピン代わりをつけてみます!
教えていただき、本当にありがとうございます。
いつもお世話になっている釣り仲間のおじさんというか、おじいちゃんがいまして、その人オリジナルのスピナーベイトを作って渡しあげたいなとがんばっているんですが、毎日問題が発生していまして。。。
多分、真鍮を切削する1番最終の動作のときに、実物のストックのトップの高さがFusionのデータより高くなっていて、エンドミルがストックに余計な負荷をかけてしまっているように思います。そのために、真鍮が反り上がるように曲がっているんだと思います。現に、1番最初の動作で、結構彫り込んでしまっている箇所があり、実物のトップの高さにもバラつきがあるように思います。
教えていただいたように、アルミを捨板のように使いたいと思いますが、両面テープは、どこのメーカーの商品で、どれくらいの厚さのものを使われていますでしょうか?
また、パス設定で、公差は0.001mmくらいに設定されていますでしょうか?
真鍮板の切断面がきれいに切削されておらず、公差なのか他の設定を変更した方が良いように考えています。
タカさんが頑張って作ったスピナーベイト、おじいちゃんも喜ばれるでしょうね。
完成が楽しみですね。
ストック高さのバラつきで一発目が深く加工される場合は、ストックより少し上から加工が始まるようにCAMの設定(トップ高さ)を変更してあげれば解決すると思いますよ。
どのくらいバラつきがあるのか分からないのでなんとも言えないですが、ストックより0.2mmくらい上から加工開始すれば大丈夫ではないですかね。
一発目が全くストックに当たらないかもしれませんが安全です。
両面テープは特にどのメーカーというのはありません。
スポンジ付き等の厚手のタイプでなくて普通の薄いタイプの強力タイプならどこのものでも良いと思います。
貼る時は適当に貼るのではなく、加工するパーツの下にくるようにテープを貼りましょう。
パーツの下だけに貼るというようなケチな事をすると加工中に動いてしまう事もあるので注意して下さいね。
公差は大体0.01ですね。
厳しくしても0.005です
一昨日、昨日はありがとうございました。
教えていただいたように、ポケット除去を試してみたら、問題なく加工できたのですが、穴加工などのように、Z軸方向の動きが必要になるものだとやはりズレてしまいました。
型でプレスするために、位置決め用のピンとそのための穴が必要になるかと思いますが、穴はどれくらいの直径と深さを切削されていますでしょうか?
また、位置決め用のピンはどんな素材を使い、直径何ミリのものを使われていますでしょうか?
どうぞよろしくお願い致します。
ポケット除去、上手く加工できたようで良かったですね(^^)
位置決め用のピンは平行ピンのφ3を使っています。
穴加工ですがQT100でZ軸を垂直に加工(ドリル加工)するのは厳しいですね。
回転が止まってしまうか、ステッピングモーターが脱調してしまいます。
主軸のパワーが弱すぎるのが原因です。
なのでφ2のエンドミルで2D輪郭か2Dポケットを使用してφ3の穴を3mmくらいの深さまで加工しています。
この3mmの深さの穴を案内にしてボール盤を使って深く仕上げています。
ボール盤をお持ちでないのでしたら、ピンにこだわらずに型に凸形状と凹形状を直接削って作る方法もありますよ。
大変ありがとうございます!
実は、今日、ブレード用の真鍮1個を真鍮板からくり抜くために、直径2mmフラットエンドミル(アルミ用)&オイルを使ってポケット除去で切削していましたら、30分くらい経ったときにエンドミルが折れてしまいました(涙)
切削条件は、切削速度200で最大粗取り切り込みピッチは0.03mmで割と安全に設定したのですが、それでも折れてしまいました。
ポケット除去は負荷制御よりも負荷が大きくなりやすいので、仕方ないかなと思ってはいるのですが、真鍮板から薄皮1枚を残してくり抜く場合は、切削ピッチなども特別に設定する必要がありましたでしょうか?
アルミや真鍮の場合は、ポケット除去の前に負荷制御などをされてからポケット除去に移られていますでしょうか?
ご紹介いただいたフラットエンドミル2mmを購入しようと思っていまして、そのフラットエンドミルだと、ポケット除去でもエンドミルは折れにくいですかね?
ポケット除去?
という事は必要な部分以外は全て削ってしまっているのですか?
切り抜き加工の場合は、2D輪郭加工が適していますよ。
2D輪郭だとパーツの外周部分だけを削るので無駄な切削が減って時間短縮になりますし刃物の寿命も延びると思います。
私が使っている刃物で真鍮を削って破損したのは、加工中にパーツが外れてしまって派手に巻き込んでしまって折れた時の1回だけですね。
今使っている刃物は3本目ですが、もう1本は長く使ってバリが酷くなって交換しました。
ありがとうございます。
3Dポケット除去を採用したのですが、「形状」の「加工境界選択」で、ブレードの外周にあたる部分だけを切り抜くようにして切削してみました。
切り抜く場合は、3Dポケット除去(加工境界設定有り)よりも2D輪郭加工の方がエンドミルへの負荷が小さくなるものでしょうか?
monchiさんがクローラー用の部品をアルミから切削されている動画を見たとき、結構勢いよくアルミを削っていたように見えたのですが、私がやった3Dポケット除去での切り抜き加工も同じような勢いのある動きで、2D輪郭加工と3Dポケット除去での切り抜きは、負荷は変わらないのかなと思いました。
そうすると、私が使用したフラットエンドミルが弱かったか、フライスそのものが十分に回転していないのか、そこへんを検討する必要がありますかね。
外周部分だけの切削でしたら2D輪郭も3Dポケット除去も負荷は変わらないと思います。
私の加工条件との違いは送り速度と切り込み量と刃物ですよね。
送り速度と切り込み量は、私の設定より落としていますので問題はやはり刃物の違いかもしれません。
刃物の刃長が長すぎる場合などは、もっと条件を落とさないとダメな事もあります。
刃長が長くなるほどビビリも発生しやすくなるし折れやすくもなります。
ちなみに私の使っているφ2(AL2D 2DLC)の刃長は4mmです。
AL2Dの2Dは刃径の2倍という事です。3Dだと3倍ですね。
刃物の溝のねじれの角度も負荷に影響がありますし、コーティングの有り無しで寿命に違いが出ます。
その辺も関係があるかもしれません。
やはり同じ刃物を使って頂く方が問題が分かりやすいかなと思います。
本当にありがとうございます!
ちなみに、エンドミルは直径3mm以上のものは使われますでしょうか?
直径2mm以内でどの工程も切削した方がトラブルなく切削できるでしょうか?
金属(アルミ•真鍮)は特に理由がない限りは2mm以下で加工しています。
QT100は主軸のパワーが弱いので大きい径のエンドミルを使うメリットはあまりないと思います。
2mmと3mmだと負荷も大きく違うということはないので同じ条件で加工しても大丈夫だと思いますが、それ以上径が大きくなると加工条件を落とさないと主軸が止まってしまったりして逆に効率が悪くなります。
それに、径が大きくなるということは削り残しも多くなります。
仕上げの負荷を考えると削り残し加工の追加など工程を増やす必要も出てきます。
工程が増えたり負荷が大きかったりすると、その分ミスやトラブルの可能性も上がると思うので、それだったら最初から小径の刃物で加工した方が面倒くさくなくて良いというのが私の考えですね。
シンプルに安全にで加工しています。
ただ、この辺の考えは人それぞれだと思います。
「俺は常に限界を攻めるぜ!」
という人もいるでしょうし性格で違いが出るところかもしれませんね。
ちなみにですが、A7075で真鍮をプレス出来るのか凄く興味があるので、良かったら結果を教えて貰えると嬉しいです。
大変ありがとうございます。
凹凸の型、それぞれ3mmの深さを掘って、5.5〜6mmのピンを間に挟む感じでも位置決めとしては問題ないですかね?
それとも、ピンが型を貫通していないとプレスするときに問題が起きやすいでしょうか?
ピンを使うのでしたら片側は圧入して固定すると思うのですが、それだと深さ3mmでは浅すぎると思います。
出来れば直径の倍以上は欲しいところですね。
ピンが型を貫通してしまうのもダメです。
ピンが邪魔になってプレス出来なくなりますよ。
説明が下手で分かりにくかったかも知れませんが、型に凹凸の形状というのはアルミ型の片方にピン形状(ピンの代わり)を追加、もう片方に穴形状を追加して位置決めをしてみてはどうか?
という事です。
私はシリコン型はこの方法で位置決めしています。
この記事の一番最初の画像のイメージです。
このシリコン型をアルミ型と思ってください。
本当にありがとうございます!
はい、プレス用の型をアルミでつくりたいと考えています。
少し前に、別の用途で、QT100を使ってアルミのA7075を負荷制御で削ったときに、本来削れるはずの深さよりも1mm分浅くなってしまっていました。
ボールエンドミルで負荷制御をしたので、切削する力が上に逃げてしまい、うまく削れなかったのかなと思っているのですが、QT100の場合は、負荷制御よりも、フラットエンドミルで3Dポケット除去の方がよろしいものでしょうか?
もしくは、A7075を切削するには、QT100だと難しいものなのでしょうか?
できれば、A7075で型を削りたいと考えていまして、monchiさんがもしA7075またはA2017を削れられたことがありましたら、その際に気をつけておられたことを教えていただけますと幸いです。
どうぞよろしくお願い致します。
A7075を使っているんですね。
それだと硬度的は真鍮と同程度か少し高いくらいだと思うので型にも使えそうですね。
私はA2017は良く使うのですがA7075は使ったことがないのでQT100で加工可能かどうかはちょっとわかりません。
ちなみに、私はQT100でA2017を粗取り加工する時は以下の条件で加工しています。
フラットエンドミル:φ2(アルミ用DLCコーティング有り)
切り込み量:0.1mm
送り速度:F400
加工方法:3Dポケット除去
真鍮を加工する時は切り込みを0.05に変更して他は同じ条件で加工しています。
エンドミルも粗取りではフラットエンドミルしか使いません。
負荷制御はZ方向の切り込みを増やして側面の切り込みを減らして(薄く)負荷が均一になるように削っていく方法だと思うのですが、QT100のように剛性も低く加工速度が遅い機械だと加工時間が余計に掛かると思います。
が、この辺は好みもあるので目的が達成できればどの方法でも構わないと思います。
仕上がり寸法が1mm浅くなっていたのはおそらくですがZ軸のステッピングモーターの脱調が原因でないかと思います。
負荷による刃物の逃げにしては流石に1mmは大きすぎるような気がするのですが…
私は加工条件は基本的に安全を優先しています。
刃物や材料も結構高価ですから刃物が折れてしまったり加工失敗になって再購入するとかなりの痛手です。
本当にありがとうございます!
刃は購入しまして、届いたら試してみたいと思いますが、真鍮の素材まではあまりこだわらず、普通に売られている真鍮を使われていますかね?
真鍮の薄皮0.06mmを残すのは難しいかと思いますが、土台となるアルミ&両面テープ&真鍮を接着したストックの高さを図る際に気をつけておられることはありますでしょうか?
真鍮板はホームセンターなどで普通に入手できるもの(C2801P)を使っていますよ。
高さを測る時、加工範囲が狭い時は特に気にしませんが、広い場合は加工範囲の4隅かそれ以上の場所で高さを確認してからどこを基準(Zのワーク原点)にするか決めています。
一番高い所にするのか?低い所にするのか?もしくは中間の所にするかはその時のバラつき具合で判断しています。
真鍮はアルミに比べると硬いので、あまり薄皮を残しすぎると板から切り離すのに苦労するので結構ギリギリを攻めます。
なので薄皮がめくれて破れてしまう所もありますが、パーツの下にしっかり両面テープが貼られていれば大丈夫です。
刃先に両面テープが付着したりしますが、極少量なら何とか大丈夫です。
monchi さま
ご丁寧にありがとうございます。勉強になりました。
先日もありがとうございました。
徐々に型と真鍮が出来上がってきたのですが、位置決めとして、直径3mmの平行ピンを刺すためにアルミ型に穴を空ける際、3.05mmまたは3.1mmくらいの直径の穴が良いでしょうか?
順調そうで何よりです。
おじいちゃんの笑顔がみられるのも近そうですね(^^)
平行ピンを入れる穴径はピンを圧入するのかしないのかで変わります。
私は圧入するので2.98〜2.99で仕上げますね。
もちろん圧入する方の型だけです。
もう片方の型には3.05で加工します。
圧入する深さはオス型の一番高い所よりもピンが数ミリ出っ張るくらいにしています。
プレスする時、プレスされる素材にオス型が当たる前に、ピンがもう片方の型の穴に入っていないと位置決めが出来ないからです。
圧入しない場合は両方とも3.05でいいと思いますよ。
ただ、この場合はピンがゆるゆるなのでピンが抜け落ちないように(ズレないように)狙った深さ(止まり穴)で穴を加工する必要があります。
教えていただき、ありがとうございます。
挙げていただいた、可能性の問題点を検証してみたいと思います。
はじめまして。「シリコン型用の原型」というキャプションがついた写真について質問させてください。
この白い(ベージュ)物体の素材は何ですか?
削る前はどのような形状なんでしょうか?
写真の片方をひとつ作るのにどれくらいの時間がかかりますか?
以上,お手すきの際に教えていただけると幸いです。
どうぞよろしくお願いします。
Yamashitaさん
はじめまして
コメントありがとうございます。
ご質問の原型の素材ですが、私はレジンキャストを使用しています。
2液性のウレタン樹脂です。
これを適当な大きさのタッパーに流し込み硬化させてから取り出して使用しています。
ですので加工前の形状はタッパーの形そのままです。
少しコストは上がりますがケミカルウッドという材料もあります。
試作品を作る時によく使われる素材です。
私は使った事は無いのですが、おそらくこちらの方が使いやすいと思います。
加工時間は加工する物の大きさや、仕上げの細かさ、機械の性能(機械剛性や最高速度)で変わってくるので一概には言えないのですが、私の場合だと原型の片方で1日というのが多いですね。
お役に立てたか分かりませんが参考にして頂ければ幸いです。
ご丁寧にお答えいただき、ありがとうございます。
まず7075で正確な型ができるように試行錯誤してみます!
型ができて、プレスしました、結果をお伝えしたいと思います!
本当にありがとうございました。
コメント失礼します。
CNC加工機の値段を知りたいです。
また
趣味の範囲でしたらCAD設計〜CNC操作設定ソフトを無料でインストールできるようですが
家庭用ノート型パソコンでも
ソフト自体の容量は、遊べる範囲で充分なんでしょうか?
よろしくお願いします。
進藤博喜さん
こんにちは
コメントありがとうございます。
質問のCNCフライスの値段ですが、私の使っているオリジナルマインドさんのKittMill-Qt100(生産終了)でしたらオプション品まで入れて約26万円位でした。
同社の製品でしたら、本体価格がQt100より5万円程高くなっていますが、同等品でKittMill-CL100というのがあります。
X,Y軸のストロークが長くなっている以外は、同じ仕様です。
CNC制御用ソフトウェア ( USBCNC )も含まれていて、使い方(設定)も分かりやすく解説されてます。
Amazonなどで中国製の安い(2万円台~)がありますが、使い方が分からなかったり問題があった時に自力で対処できるならこちらの方がかなり安いのでお買い得だと思います。
部品のスペック的には、私の使っているCNCフライスよりかなり上です。
が、組み立て後の精度は分かりません。
私の場合は、安心を買ってメーカーがしっかりしている国産品を選択しました。
無料のCADCAMは、Fusion360になると思います。
推奨スペックはこちらを参考にしてください。
ノートパソコンでも大丈夫ですが、CADCAMは複雑な演算を膨大に行いますのでハイスペックに越したことはありません。
私も普通の?ノートパソコンで使用しています。
ちなみに私のCADCAM用パソコンのスペック
Corei7-8750 2.2GHz
RAM 8GB
グラフィックボード GEFORCE GTX
です。
どこまで低スペックでも大丈夫かは、私にはお答えできないです。
”Fusion360 スペック”で検索すると、他にも情報がありますので読んでみる事をお勧めします。
CNC制御用ソフトウェアは無料ではありませんが、CNCフライスを購入するとコントローラーとセットで付属されている場合が多いと思います。
付属されていない場合は、ソフトをダウンロードして別途ライセンスの購入が必要かもしれません。
こちらは、パソコンのスペックは低くても問題ありません。
私がCNCフライスと接続しているパソコンは年代物のWindowsXPです。
ちょっと長くなってしまいましたね。
ごめんなさい…
コメント失礼します。
はじめまして、タカと申します。
とても興味深く、記事を読ませてもらっています。
わたしもKitmill QT100とFusion 360を使って、スピナーベイト用の真鍮ブレードをアルミ型で作りたいと思っていますが、アルミ型を作る場合、3Dポケット除去→3Dフラット→走査線といった順番で切削していった方が良いのでしょうか?
タカさん
はじめまして
コメントありがとうございます。
真鍮ブレードをアルミ型で作りたいとの事ですがプレス型のことですよね?
これは少し厳しいかもしれません。
アルミより真鍮の方が硬度が高のでアルミ型が負けてしまう可能性があります。
アルミもA2017(ジュラルミン)以上を使って、真鍮の厚みが薄ければ少しは使えるかもしれませんが寿命が短いかもしれません。
加工手順は私なら•••
オス型
3Dポケット除去(粗取り/フラットエンドミル)
走査線加工(中仕上げ/フラットエンドミル)
走査線加工(仕上げ/フラットエンドミル)
(走査線加工は垂直パスを追加で)
メス型
2D面(上面/フラットエンドミル)
3Dポケット除去(粗取り/フラットエンドミル)
スキャロップ(中仕上げ/ボールエンドミル)
スキャロップ(仕上げ/ボールエンドミル)
の手順で加工すると思います。
形状によっては違う手順になるかもしれないですが基本はこの流れで加工しています。
参考にしていただければ幸いです。