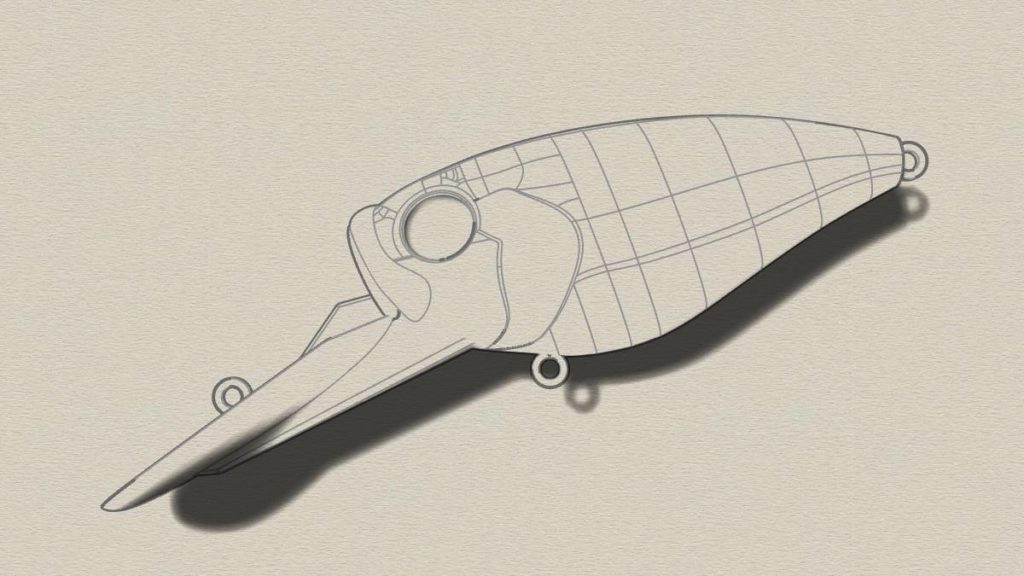
前回は、簡単にCNCフライス加工について説明しました。
今回は、CADを使ってどういったルアーの原型を作ればいいのかを説明していきます.
最初に申し上げておきますが、CADの操作方法の説明などは一切しません。
お使いになっているCADの使い方などを検索してモデルを作れるようになっておいてください。
CADの前に実物大で紙に描くこと!
CADで描けるのにどうして?
と思われるでしょうが、パソコンの画面上で見ても実際の大きさは実感できません。
削りだしてみてから、「あれっ、思ってたより小さい」とかになってしまいます。
実際に作りたい大きさを紙に描いた方がイメージが掴みやすいです。
紙に描いてイメージが掴めたら、その寸法を測ってからCADでモデリングしていきます。
CNCフライスで加工する事を考えてモデリングする事!
CNCフライスを使ってルアーを作るのだから、あんな形にしたいとか、複雑なデザインのルアーを作りたいとか当然思っていますよね。
しかし、残念ながらどんな形状でも加工できるわけではありません。
CNCフライスは便利ですが万能ではなくて、出来る加工、出来ない加工というものがあります。
例えば、
アンダーカット形状は加工出来ない
アンダーカット形状といって、刃物が削れない領域を作ってしまうと削り残しができます。
削り残しならまだいいですが、必要な部分を削り取ってしまう可能性もあります。
最悪、刃物の破損もありえます。
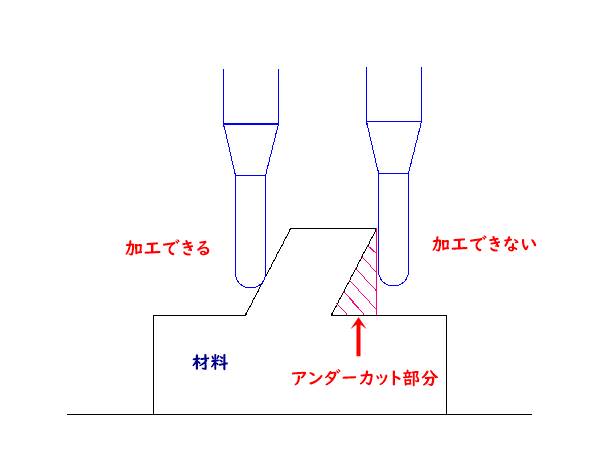
絵が雑で申し訳ないですが、赤斜線の部分がアンダーカット形状部分になります。
刃物の角度が変わってくれればいいのですが、刃物は垂直でしか加工することが出来ないので、アンダーカット部分は加工出来ないことになります。
材料の向きを変えて加工するといった方法もあるのですが、小型のCNCフライスでそれを行うのは精度的に現実的ではありません。
コーナーR
フライス加工に、コーナーRというものがあります。
製品の内角部につくRのことです。
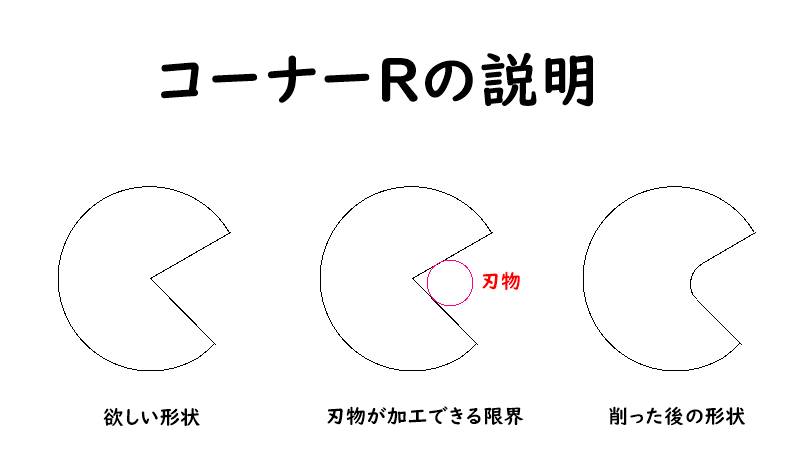
エンドミルという円形の刃物を回転させて削るのがフライス加工です。
いくらCADで角を立てたモデルを作ったとしても、刃物の半径以下の角には出来ないという事です。
出来るだけ小さいRにしたい場合は、それだけ刃物の径を小さくする必要がありますが、やはり限界はあります。
どうしても角が欲しい場合はRの部分に逃がし加工を行う必要があります。
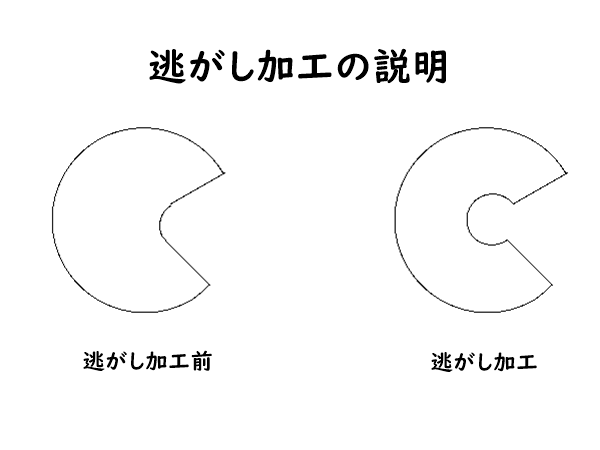
逃がし加工は、ルアー作りにはあまり必要ないかもしれませんが覚えておいて下さい。
最小R
コーナーRと同じようなものですね。
3次元形状のモデルを作った時にR形状の部分がありますよね。
その最も小さいRの事です。
ボールエンドミルを使って仕上げ加工を行いますので、コーナーRと同じく刃物の半径以下のR部の加工は出来ません。
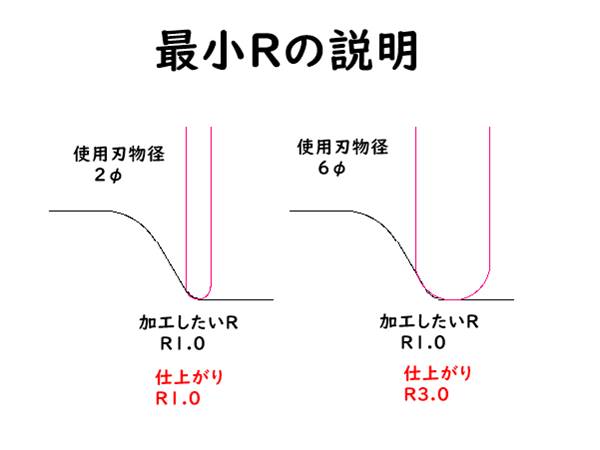
画像左が最小Rを考慮して加工した場合、右が最小Rより大きなRの刃物で加工した場合。
モデリングする時に必要以上に小さいR部分を作っても意味がないという事です。
小型CNCフライスの場合は、1φ(R0.5)位が限度ではないかと思います。
テーパーボールエンドミルというのを使えば、もっと小さいRも出来ますが刃物も高価になります。テーパー部分と製品の干渉にも注意が必要になります。
刃物の形状や刃長を把握する
2次元の薄板加工では、刃長、刃径以外はそれほど気にする必要はないのですが、それなりの大きさのルアーを3次元加工しようとすると他にも注意が必要になってきます。
刃物の形状によっては製品との干渉が発生する場合があります。
刃長、有効長、シャンクテーパー角、シャンク径などに注意が必要です。
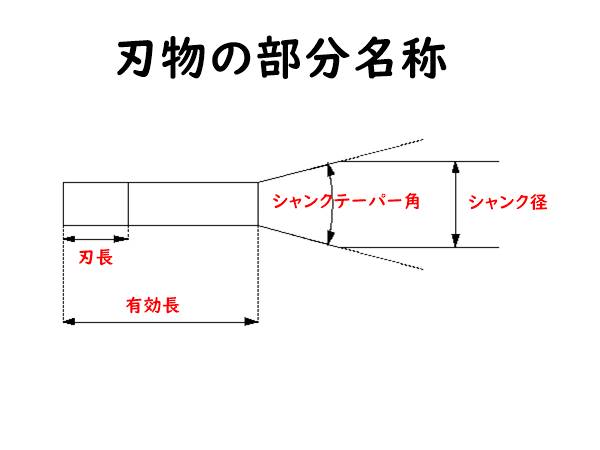
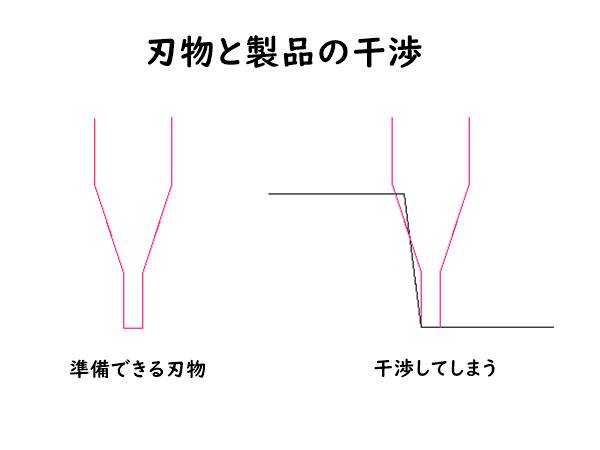
持っている刃物、購入可能な刃物で加工できるかを考えてモデリングしていかないと後で修正が大変です。
修正で済めばいいですが、最悪一から設計をやり直す羽目になる可能性もあります。
CADとは関係のない話と思われるかもしれませんが、この辺を理解してモデリングしていかないと、幾ら素晴らしいモデルを完成させても加工出来なければ全く意味がありません。
パソコン上だけでいいのなら何の制約もないですが、実際に製品を作るために設計する場合はこういった事まで考えて設計しないといけません。
完成したモデルにシリコン型用のモデルを追加する
次からは、作りたいルアーのモデルが完成しているとして進めていきます。
シリコンで両面型を作るときに、よく使われている方法として粘土を使った方法がありますが、せっかくCNCフライスで加工するのですから粘土を使わずに出来るようにしてしまいましょう。
型のベースを追加
まず、完成したモデルに型のベース(型同士が合わさる面)を追加します。
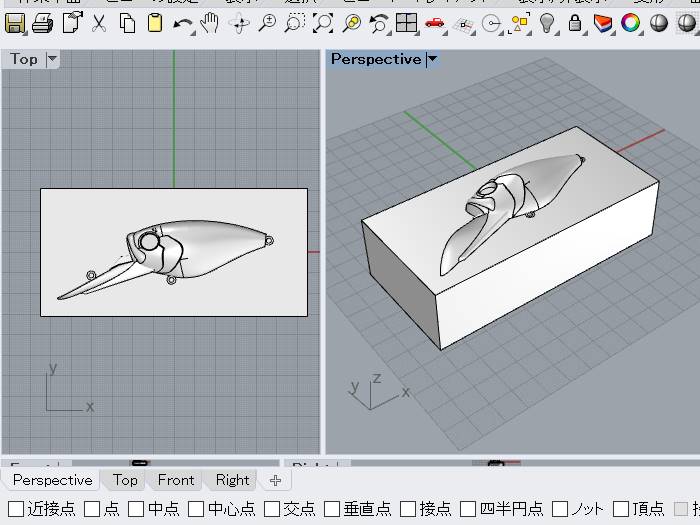
ルアーの中心にベースになる面が来るように作成してください。
湯口と空気の抜け道を追加
次に湯口と空気の抜け道を追加してください。
湯口と抜け道が、ルアー本体と接するところの面積は少し大きくしておいた方が、発泡ウレタンを流し込んだ時にトラブルが少なくなります。
狭すぎると流し込みに時間が掛かってしまい、流し込み途中で発泡しだしてしまいます。
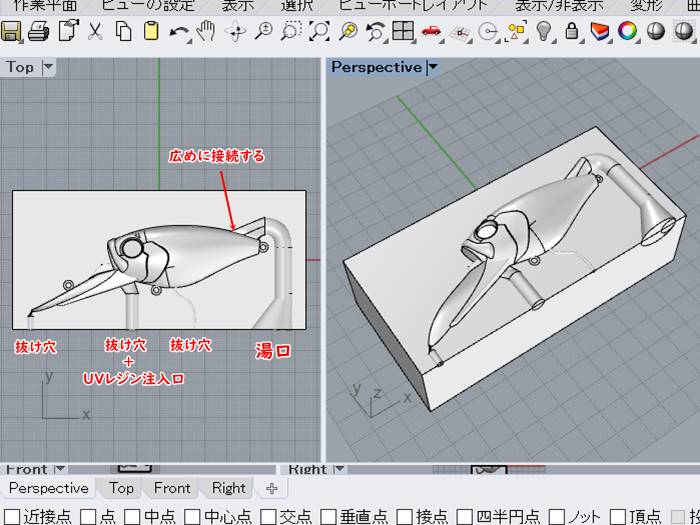
湯口から入った発泡ウレタンが、空気をスムーズに押し出していくような流れに配置するのがコツです。
写真の例は、ダメではないですがいいとも言えないのでマネしないでください。
私はUVレジンを使ってリップを作っているので、抜け穴とUVレジンを注入する穴も兼ねた部分も作っています。
位置決め部分の作成
次に、シリコン型を合わせたときに位置がずれない様にする為の形状を作成します。
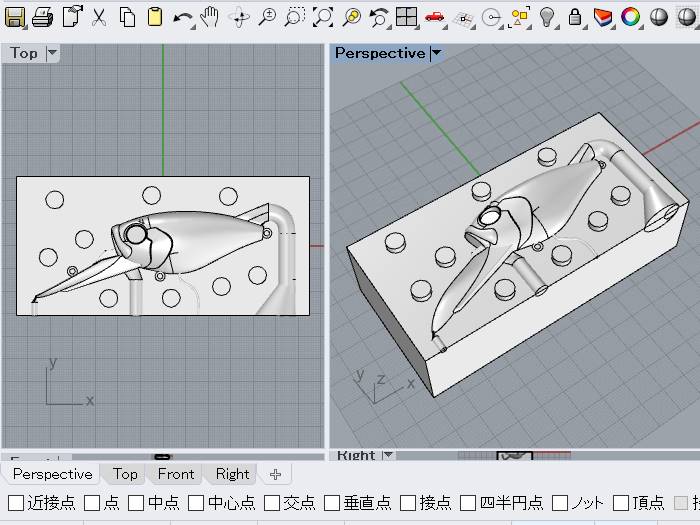
位置決め用の凸形状を作成します。
モデルでは凸形状ですが、シリコン型を作った時には凹形状に仕上がります。
この例では4mmの凸形状にしています。
アイの部分の内径部分の作成
次は、アイの内径部分を凹ませます。
どうしてかというと、ここを凹ませておくとシリコン型を作った時に、逆に凸形状になります。
この凸形状になった部分にステンレス線をセットする時、ここに引っかけて使用します。
このおかげで、型を合わせるときにステンレス線の位置がずれないようになります。
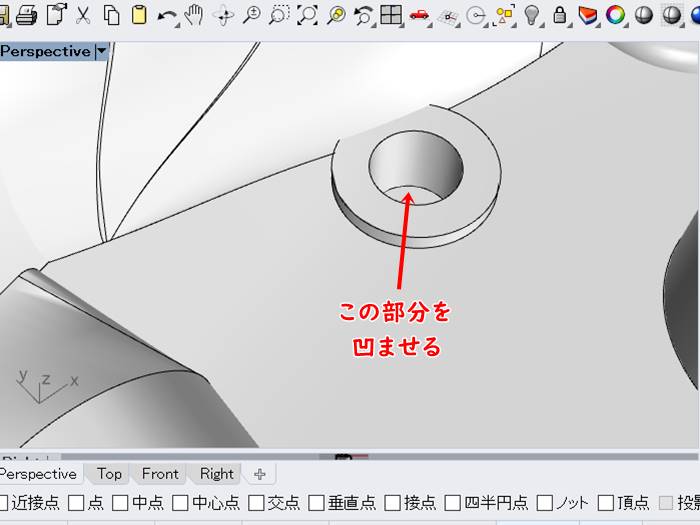
ここまでで、原型の半分が出来ました。
あと半分も同じように作るのですが少し注意することがあります。
もう一つの原型は反転(対称)した形状で作る
当たり前のことですが、同じ向きで作っても型同士が合わさりません。
今作った原型を別のレイヤーにコピーしてから反転(対称品)させて下さい。
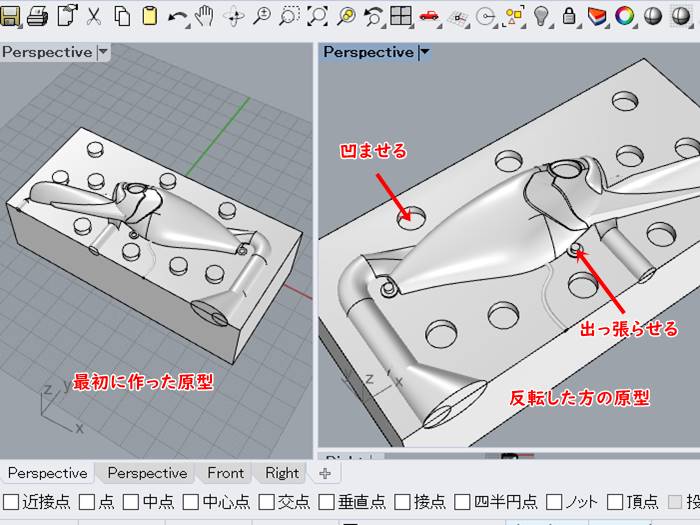
ただ反転させただけでもダメで、
位置決め用の凸形状だった所を凹形状に変更する。
アイの部分の凹ませた部分を凸形状に変更する。
という作業がいります。
これでシリコン型を合わせたときに凸凹形状が噛み合って、位置決めが出来るようになります。
最後に、CADのTOP画面から見たときに、このように見えるようにモデルを配置して下さい。
その際に、X0、Y0の位置に加工原点が来るようにしてください。
画像の例ではモデルのX,Yの中心に加工原点が来るように配置しています。
CADのX0、Y0の座標の位置が加工原点になります。
Zの位置はベース面がZ0の位置に来るように配置して下さい。
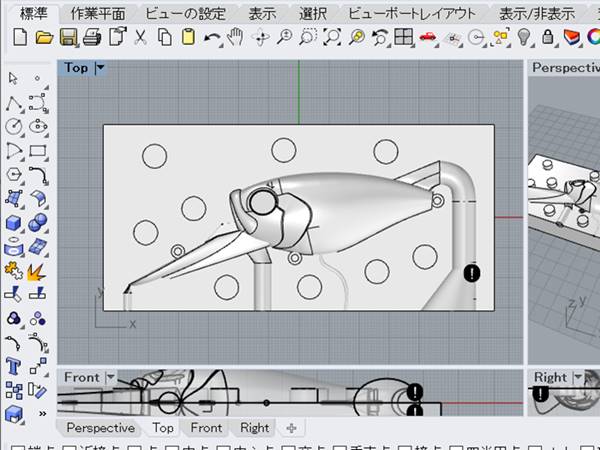
これで、CAMに渡す前のモデルは完成です。
お疲れさまでした。
簡単な説明なので、分かりにくいところもあると思いますが、CADで作図する際の注意点と手順を説明させてもらいました。
コメント