前回までは、パソコン上での作業でしたが今回から実際の加工に入ります。
加工する材料や刃物を準備しておいてくださいね。
小型とはいえ、回転する刃物を使用する立派な機械ですから安全には細心の注意を払ってください。
USBCNCについて
USBCNCとは、パソコンを使用してUSBケーブルでつながれた機械側(コントローラー)に指令を送る役割をするソフトです。
指令を受け取ったコントローラーが、各軸のモーターを動かします。
私が使用しているUSBCNCはバージョンがV3ですので、ちょっと古いですがやることは新しいバージョンでも同じだと思います。
USBCNCの起動ー材料のセット
まずは、USBCNCを起動させてください。(コントローラーの電源もオンにしてください)
USBCNCと機械との接続を確立させる
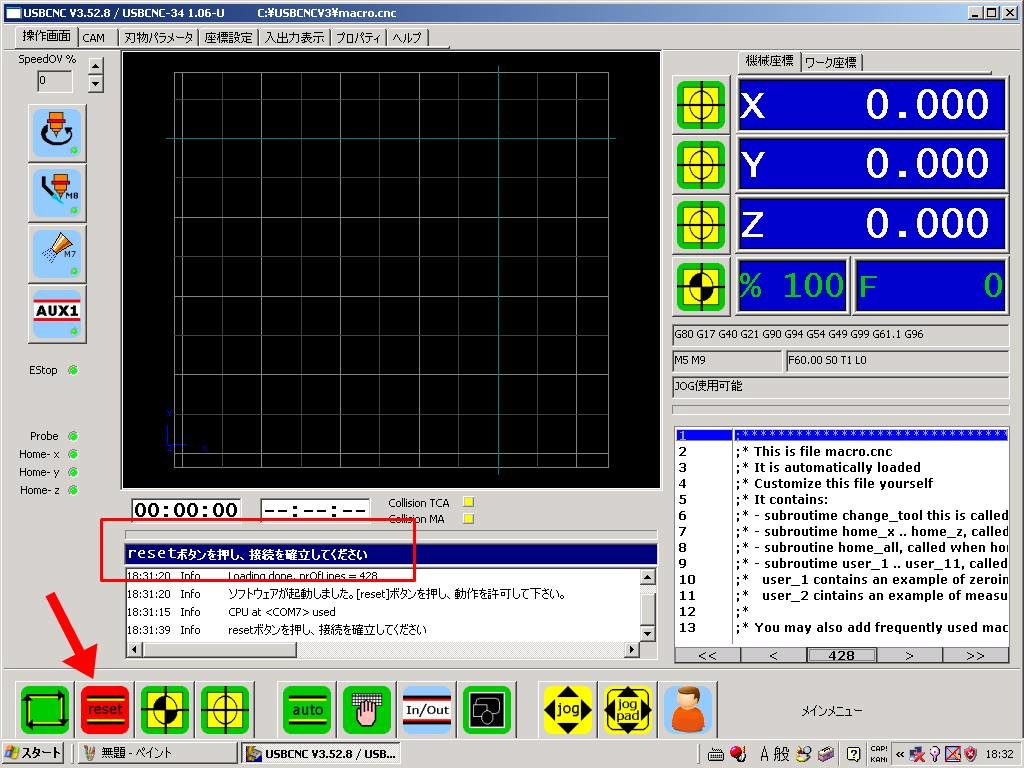
起動すると【resetボタンを押し、接続を確立してください】と表示されるので、矢印の位置にある[reset]ボタンをクリックします。
resetボタンをクリックするとUSBCNCと機械が接続され、機械から作動音がするはずです。
これで接続が確立されました。
原点復帰
まず、初めに行うことは原点復帰になります。
原点とは機械にとっての基準になる位置です(機械座標X0、Y0、Z0の位置)
原点復帰を行うと、機械に原点センサーがついていますので、その位置まで自動で移動します。
センサーが反応すると、そこで移動がストップします。
これにより、機械は毎回この位置をX0、Y0、Z0の位置と認識して動くことになります。
原点復帰をするには、矢印の所のボタンをクリックして下さい。
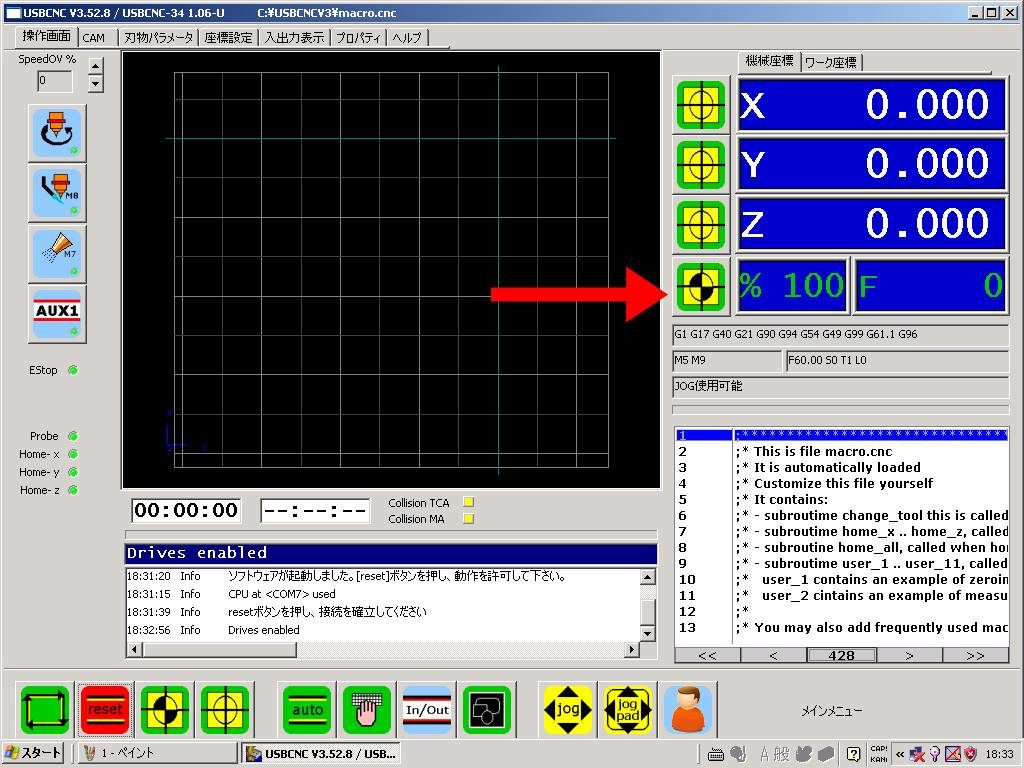
このボタンは、X、Y、Xすべての軸の原点復帰を一度に行います。
一度にといっても、安全のためにまずZ軸が原点復帰し、次にX軸Y軸といった順番で行われます。
1軸ずつ個別に行う方法もありますが、最初はこのボタンですべての軸を原点復帰させてください。
原点復帰が終了すると、機械がその位置をX0、Y0、Z0の位置と記憶します。
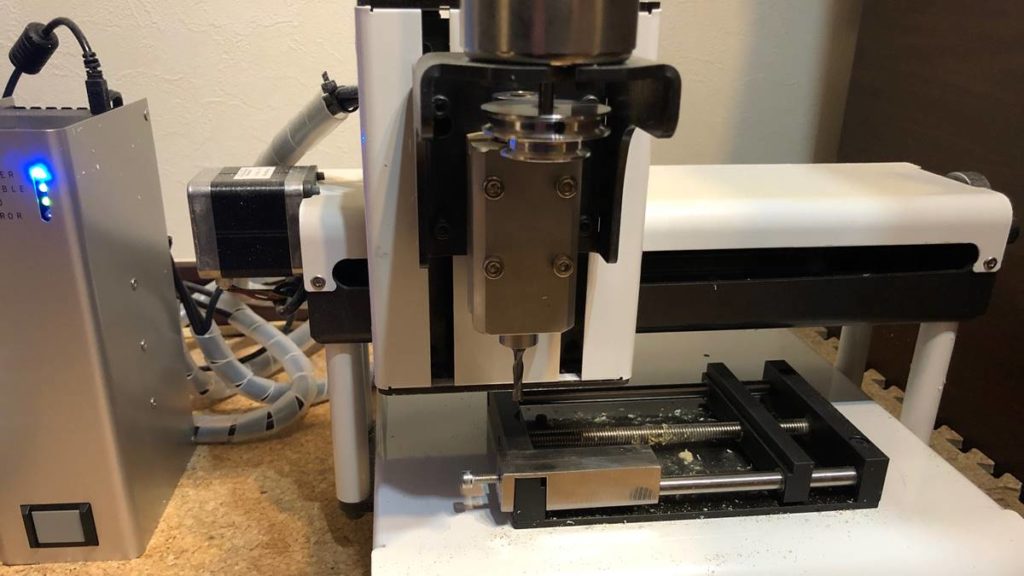
私の機械の場合は、この位置が原点になります。
左端X軸原点、手前端Y軸原点、最上部Z軸原点です。
材料のセット
まず、加工する材料をセットします。
セットする方法は、捨て板に両面テープで固定したり、バイスを使用して挟んで固定したりします。
両面テープで固定でもいいのですが、加工中にはがれてしまうリスクもあります。
私は、バイスを使用しています。

私は、レジンキャストをポリプロピレン製の容器にいれて材料を作っているので、こんな角の丸くなった材料になっています。
ワーク座標の設定
加工を始める前に、ワーク座標の設定をしなければいけません。
ワーク座標とは、加工する基準になる座標の事です。
CADで作図する時や、CAMでプログラムを作成する時に原点がありましたよね。
例では、X、Yの原点を材料の中央に、Zの原点はシリコン型の合わさる面にしたはずです。
しかし、機械側はそんなことは知りません。
加工者が、機械に教えてあげなければいけません。
Z軸のワーク座標の設定
どの軸からでも構わないのですが、とりあえずZ軸から説明します。
まず、刃物を主軸に取り付けて下さい。
その時、まだしっかりとは取り付けずに軽く取り付けて下さい。
刃物が落ちない程度で構いません。
軽く取り付けたら、材料の上まで刃物を移動させます。
移動させたら今度は、Z軸をゆっくり下げながら材料に近づけていきます。
その時、材料にぶつけてしまわないように注意しながら下げて下さい。
材料から1,2mm上で止めます。
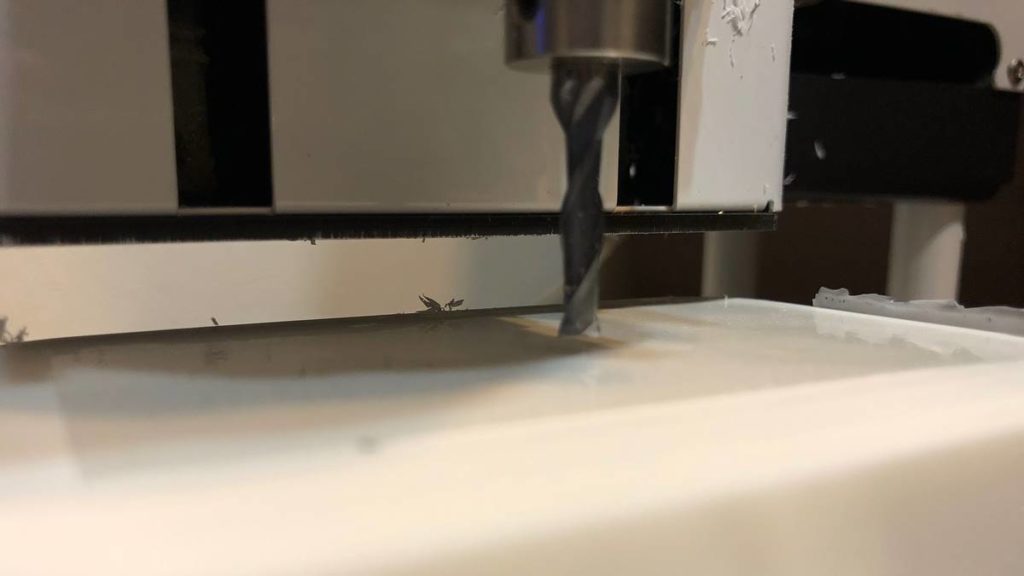
大体、この位ですね。
材料と刃物の間に僅かに隙間がある状態です。
ここで、先ほど軽く固定していた刃物を緩めて材料に当たるまで降ろします。
Z軸を下げて当てるのではなく、刃物だけを緩めて降ろしてください。

このように、材料と刃物がくっついたら今度はしっかりと刃物を固定します。
固定したら、ワーク座標のZの値を”0”にします。
矢印の部分がワーク座標を選択されていることを確認してから、赤い四角で囲ったボタンをクリックするとZ軸のワーク座標が”0”に変更されます。
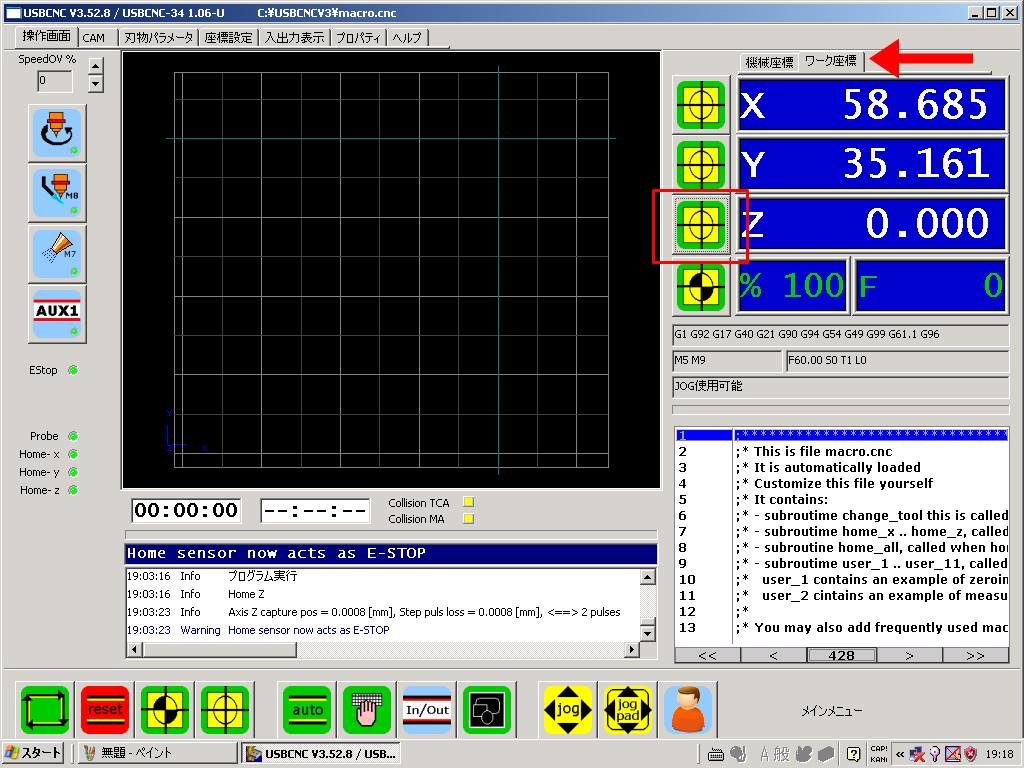
ここが原点の場合は、これで完了なのですが今回はここではないですよね。
ルアーの厚みが[7.5mm]あります。
さらにCAMで材料の設定をした時に、ストック+1mmにしました。
という事は、原点は今[0]にした位置から8.5mm下がった位置です。
一旦、Z軸を少し上げて材料から少し離れた位置に刃物を移動させてください。
移動させたら、Z軸の値が[-8.5mm]になる位置まで下げていきます。
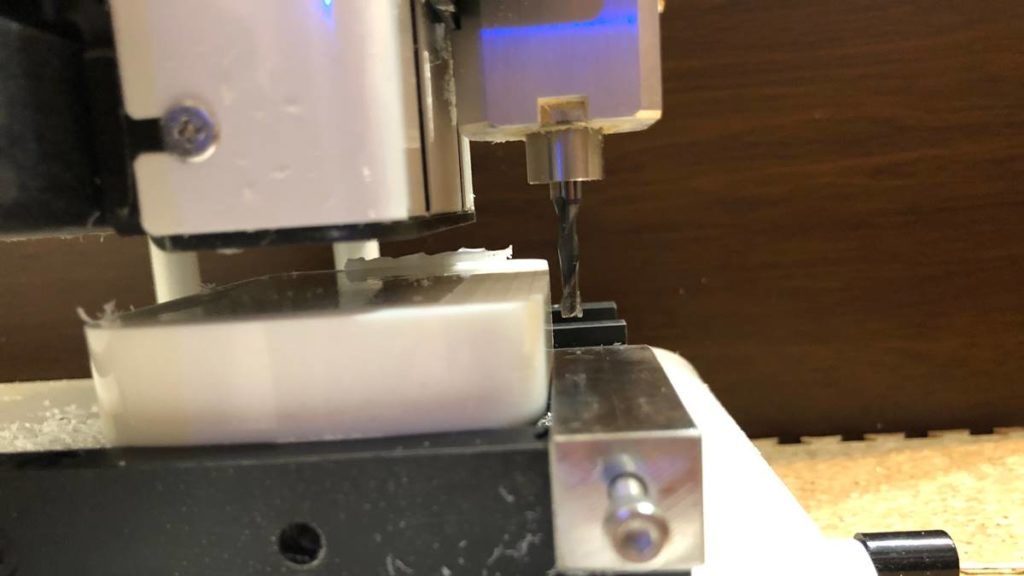
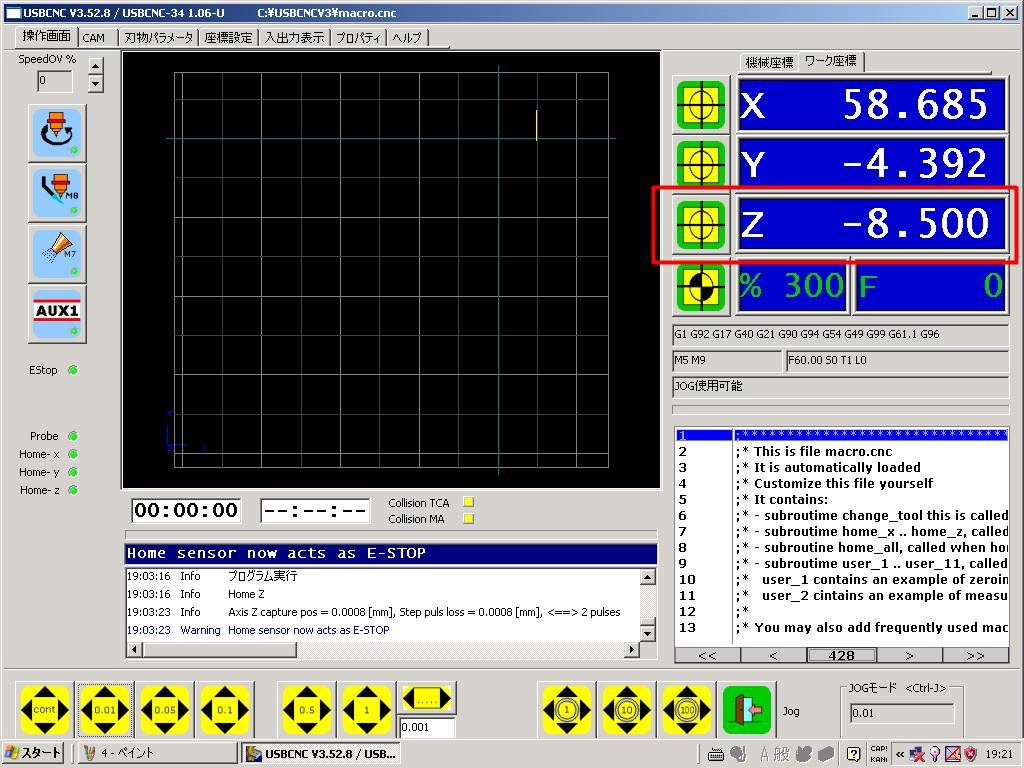
ここでもう一度、Z軸のワーク座標の値を”0”にします。
これでZ軸のワーク座標の設定は終了です。
X、Y軸のワーク座標の設定
X軸もY軸もやり方は同じなので、X軸の場合で説明します。
X軸の原点は材料の中央にしていたので、まずは中央の位置を割り出します。
まずX軸を、材料の側面に移動させます。
材料から少し隙間が空いた状態まで近づけたら、刃物を回転させます。
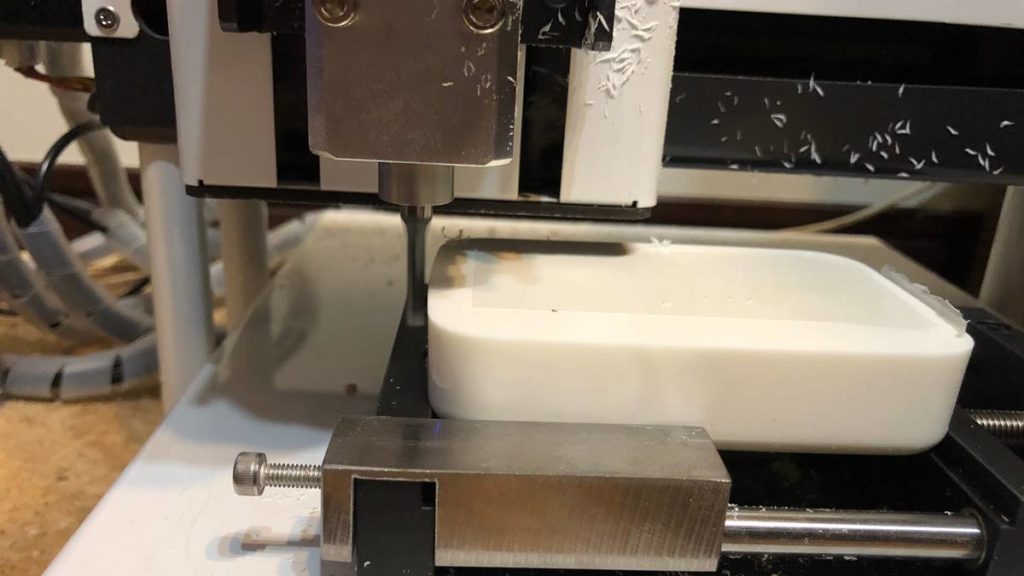
ここからJOGモードに切り替えて[0.1mm]ずつ材料の方に刃物を移動させます。
刃物が材料に当たるまで移動させてください。
材料に当たると音が変わりますので、その位置で止めます。
X軸のワーク座標を”0”にします。
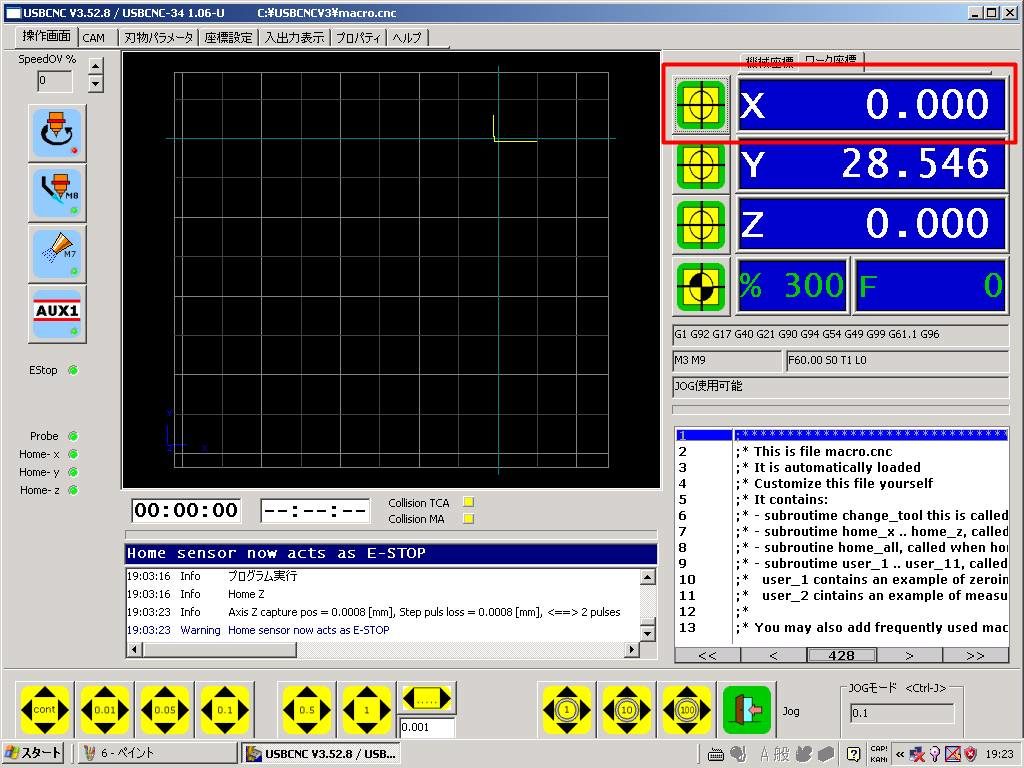
一度Z軸を材料より上に移動させます。
次に材料の右側に刃物を移動させます。
左側でやったのと同じように刃物が材料に当たるまで移動させます。
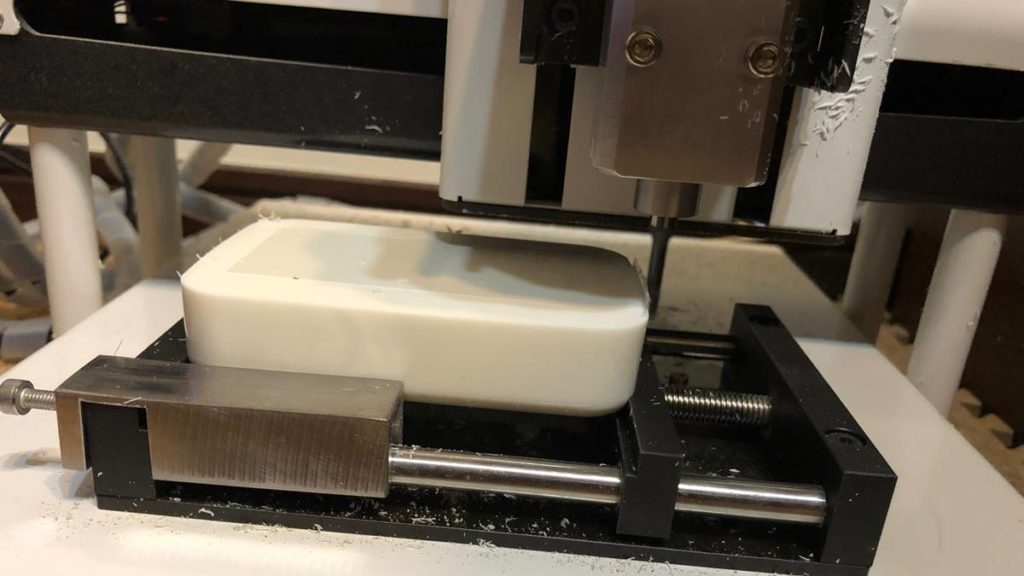
ここでX座標の値を確認します。
[102.010mm]
と表示されています。
この値の半分の位置が材料の中心になります。

刃物を[102.01mm]の半分、[51.005mm]まで移動させます。
移動させたら、その位置でX軸のワーク座標を”0”にします。
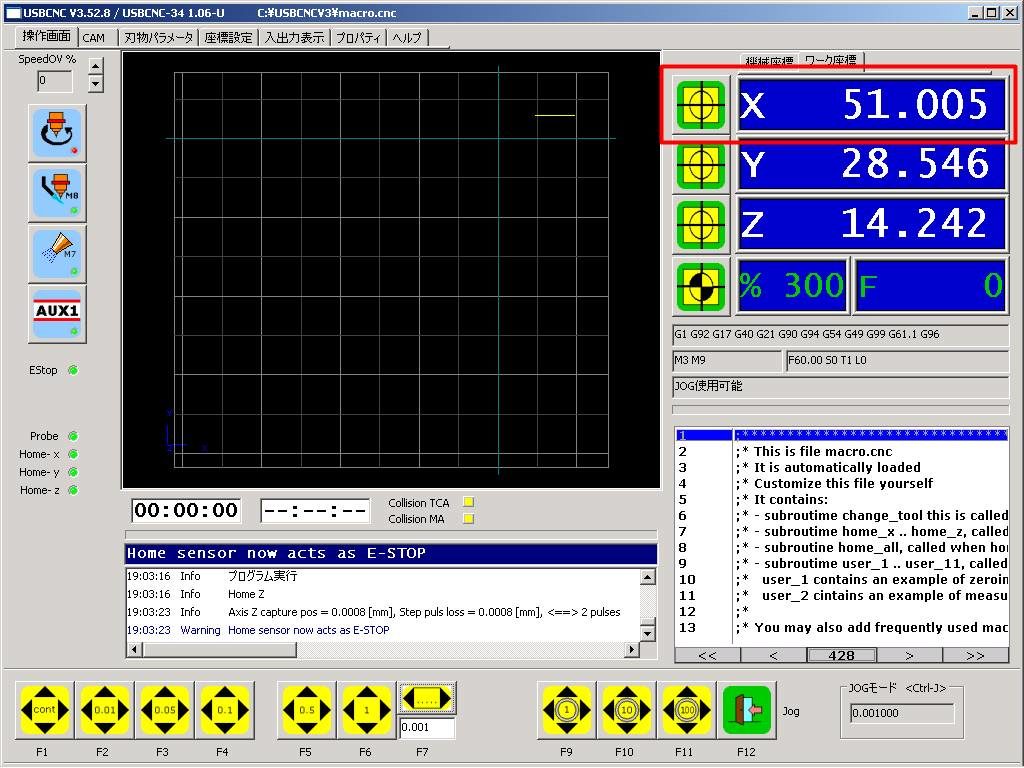
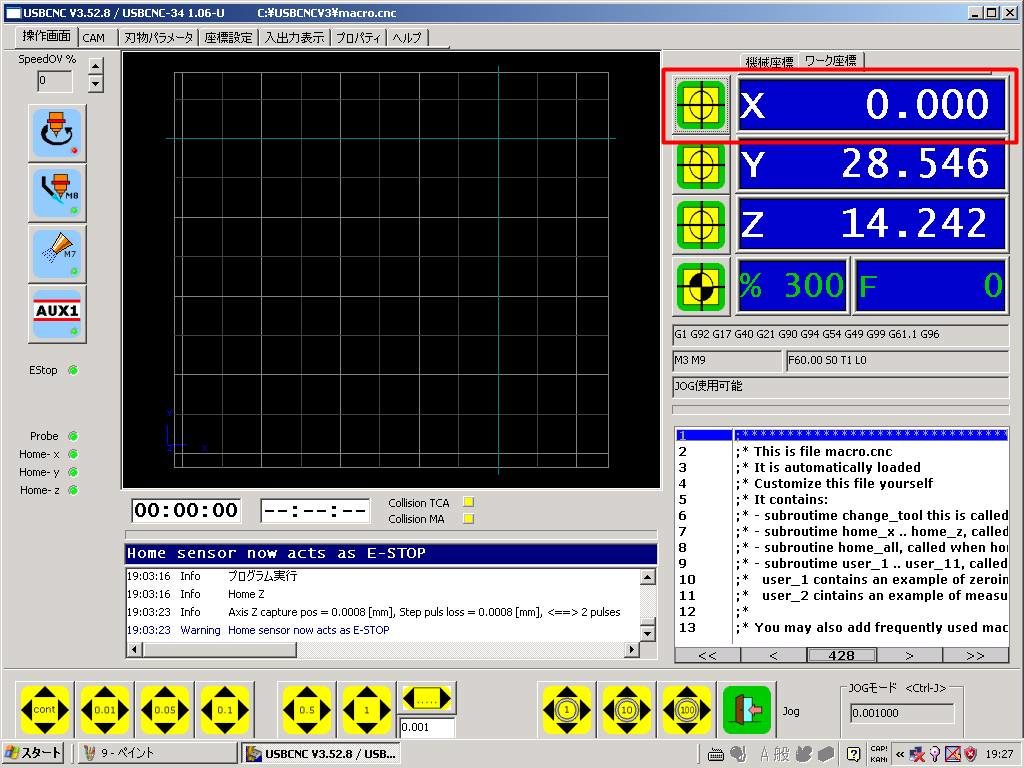
これでX軸のワーク座標の設定は終了です。
Y軸も同じやり方で設定して下さい。
X、Y軸の移動の際は、Z軸を上げ忘れて材料より低い位置で動かしてしまわないようにZ軸の高さに注意して下さい。
NCプログラムの読み込み
CAMで作成したNCプログラムを読み込みます。
読み込みが終わると、描画画面にツールパスの軌跡が表示されます。
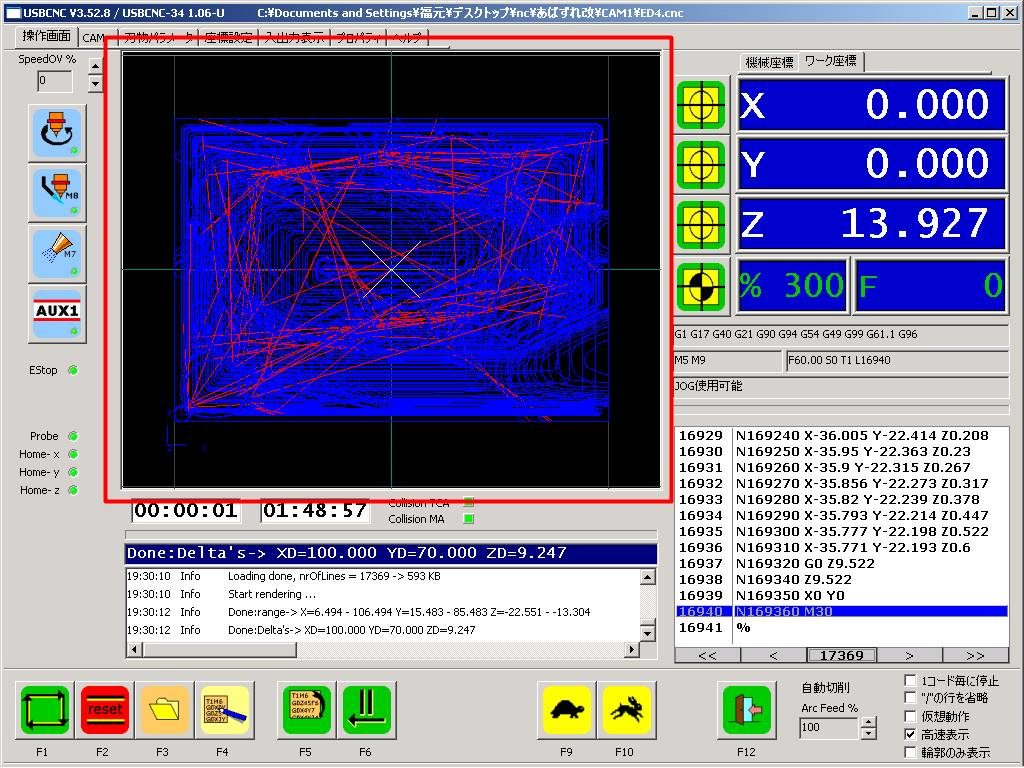
読み込みが完了した直後は、プログラム上の青いカーソルがプログラムの最後に表示されていています。
これをプログラムの先頭に戻します。
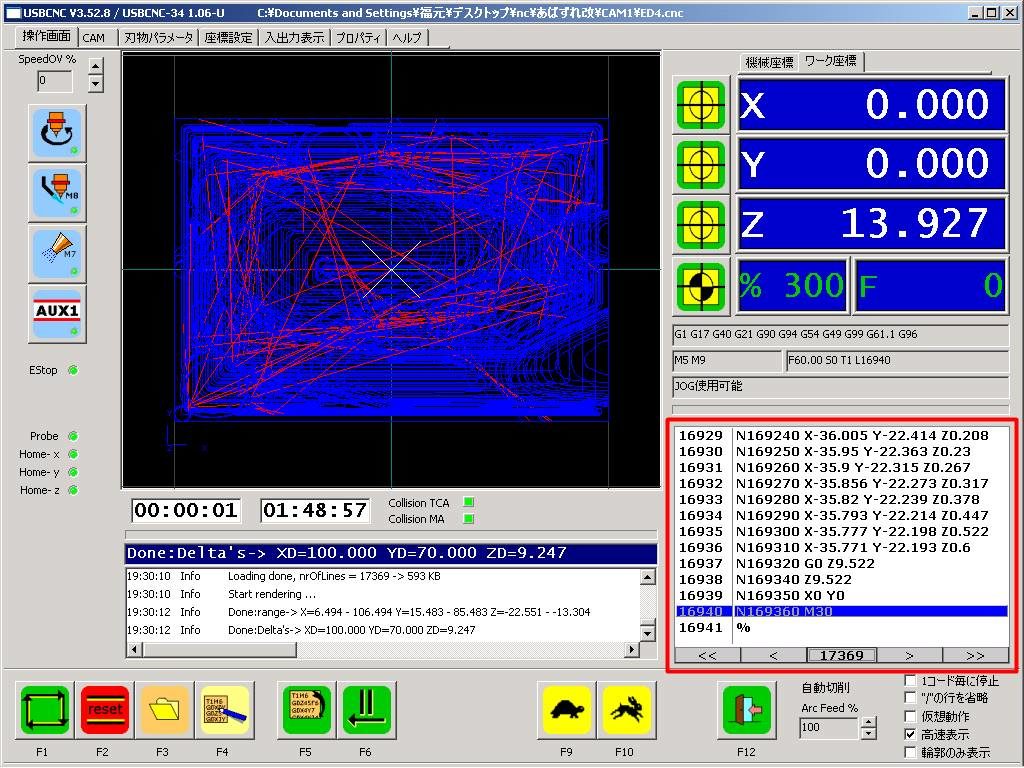
【reset】をクリックします。
プログラム表示画面が先頭に変わります。

これで加工前の準備は終了です。
加工開始
後は、画面左下にある緑の【スタート】ボタンをクリックすれば加工が開始されます。

私の機械用のNCプログラムでは、X、Yがワーク座標原点、ZがCAMで設定した移動高さの位置にに来てから、一旦プログラムが止まります。
通常はこの段階で、ワーク座標の設定が間違っていないかの確認を目視で行います。
間違いがないことを確認したら、再度【スタート】ボタンをクリックすれば、加工が再開されます。
これで後は、加工が終わるのを待つだけです。
(加工前に、材料のクランプに問題はないか、刃物はしっかり固定しているか等チェックをしっかり行ってください。)
何かトラブルが発生することもありえるので、初めのうちは機械から離れないようにしていた方がいいですよ。
加工中に、何らかの理由で止めたい場合は【スタート】ボタンを押せば一時停止できます。
再開したい場合は、もう一度【スタート】ボタンを押せば再開します。
加工を一時停止でなく完全に止めたい場合は【reset】ボタンを押せばプログラムが終了します。
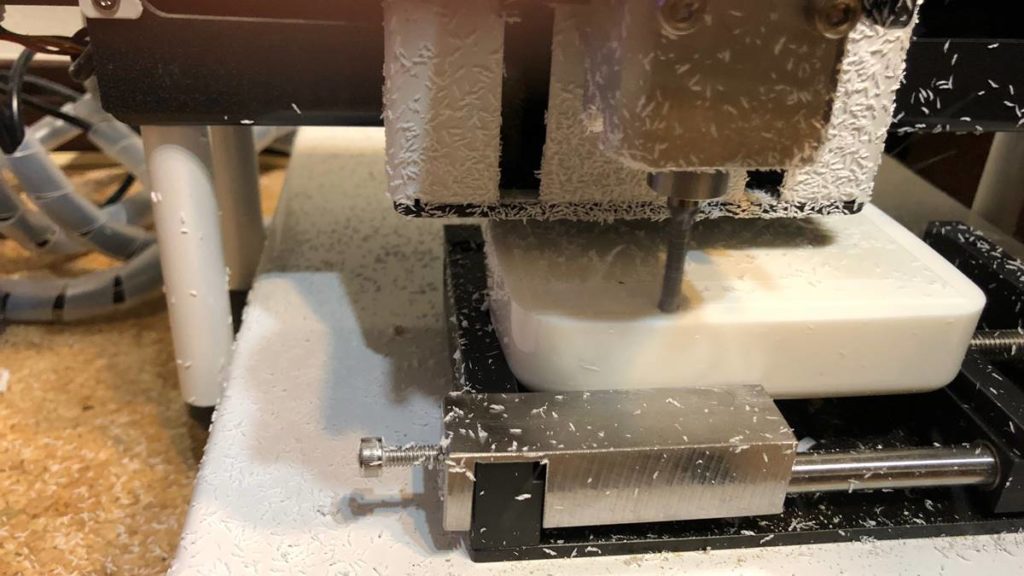
加工中です。
このように切り粉(削ったカス)が周りに飛び散りますので、散らかるのは覚悟して下さい。
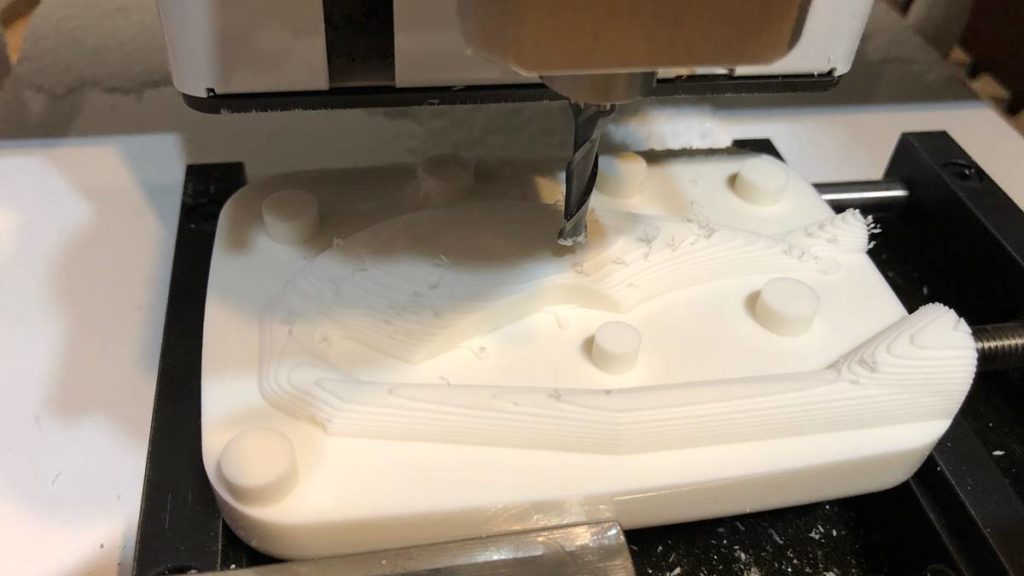
粗取りが終わったところです。
階段状に、大まかな形になっていますね。
これを、中仕上げ、仕上げと段階を踏んで加工していきます。
やり方は、いままでやったのと同じ流れです。
ですが、2本目以降の刃物の設定では、少し注意点があります。
2本目以降の刃物の注意点
ワーク座標はZ軸だけ変更する
2本目以降のワーク座標の設定は、X、Y軸の設定はしません。
刃物を交換しても、刃物の中心の座標は変わらないのでやる必要が無いのです。
逆に、やった方が位置がずれます。
X、Y軸のワーク座標はいじらないで下さい。
X、Y軸と違って、Z軸だけは再設定の必要があります。
突き出し長さが変わるので、食い込んだり、届かなかったりします。
届かない分は問題ないですが、食い込む場合は製品もダメになるし刃物の破損もありえます。
最悪、加工者がケガをする恐れもあるので注意して下さい!
下の画像は、Z軸のワーク座標の設定を忘れた場合の説明図です。
ワーク座標を変えなかった場合、機械は1本目と同じ座標で移動しようとします。
1本目で、材料の上面を[0]と設定していた場合、プログラムで[Z0]と指令すれば、刃物は上面ピッタリで止まりますが、2本目で刃物が長かった場合や短かった場合は下の画像のような状態になってしまいます。

2本目のZ軸のワーク座標の出し方
1本目の時は、まだ削る前だったので材料の上面で出しましたが、2本目以降は材料の上面は無くなっていますよね。
では、どこで出すかというと、荒取りが終わった場所のフラットな面です。
今回の例でいうと、シリコン型の合わさる面に設定していた場所です。
この場所ですね。
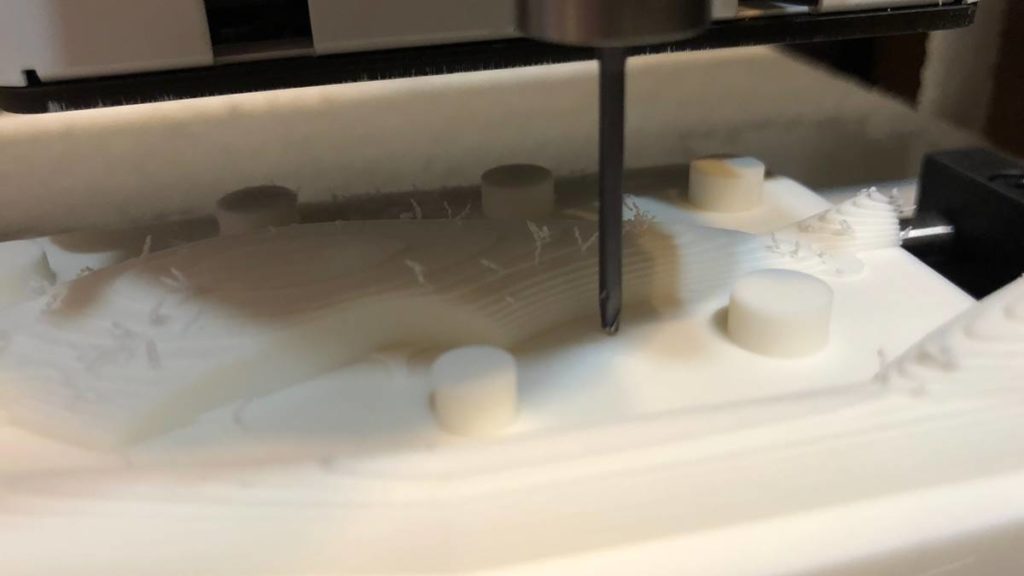
しかし、ここを”0”にして加工してはいけません。
荒取りの設定で仕上げ代を[0.2mm]残すようにしていたのを覚えていますか?
この位置は、原点より[0.2mm]高い位置なのです。
ですので、一旦この位置を”0”にした後に刃物を材料の外側まで移動させてからZ軸を[-0.2mm]の位置まで移動させます。
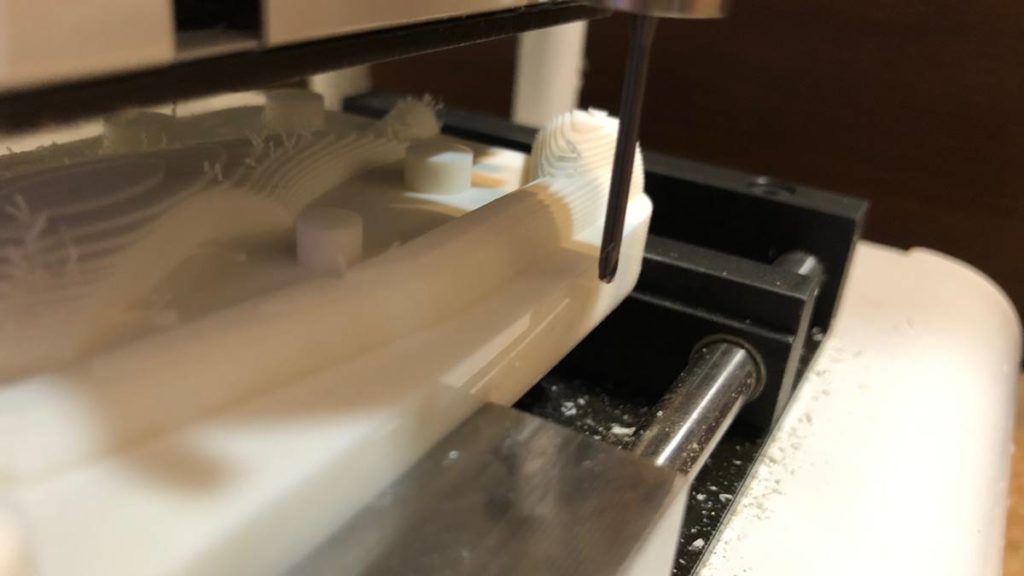
ここを、Z軸のワーク座標[0]に設定します。
これで後は、加工するだけです。
3本目、4本目でも同じです。
中仕上げが終わった状態です。
荒取りで階段状に残っていたのが綺麗になくなっています。
中仕上げの設定で、仕上げ代を[0.1mm]にしていたので、後は仕上げ加工でそれを削ります。

最後に
仕上げ加工や部分加工もやる事は同じなので説明は省略します。
どうでしたか?
上手く加工出来ましたか?
初めて、機械加工される方にとっては少々説明不足な感じもありますが、こういった物はやっぱり経験ですから失敗もしながら色々と覚えていってください。
私も、まだ分からないことはたくさんあります。
使いこなせるようになれば、ルアーに限らず、なんでも作る事が出来るので(加工できる材料の範囲で)楽しいですよ。
長々と、下手な解説をしてきましたが今回で終了です。
お疲れさまでした。
コメント